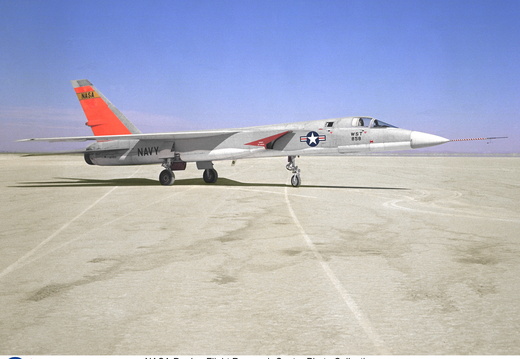
A-5A
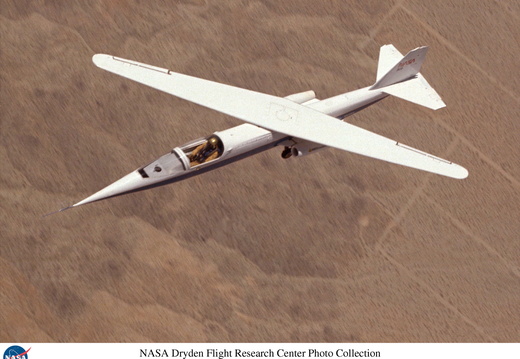
AD-1
NASA Ames Research Center Aeronautical Engineer Robert T. Jones conceived the idea of an oblique wing. His wind tunnel studies at Ames (Moffett Field, CA) indicated that an oblique wing design on a supersonic transport might achieve twice the fuel economy of an aircraft with conventional wings. The oblique wing on the AD-1 pivoted about the fuselage, remaining perpendicular to it during slow flight and rotating to angles of up to 60 degrees as aircraft speed increased. Analytical and wind tunnel studies that Jones conducted at Ames indicated that a transport-sized oblique-wing aircraft flying at speeds of up to Mach 1.4 (1.4 times the speed of sound) would have substantially better aerodynamic performance than aircraft with conventional wings.
The AD-1 structure allowed the project to complete all of its technical objectives. The type of low-speed, low-cost vehicle - as expected - exhibited aeroelastic and pitch-roll-coupling effects that contributed to poor handling at sweep angles above 45 degrees. The fiberglass structure limited the wing stiffness that would have improved the handling qualities. Thus, after completion of the AD-1 project, there was still a need for a transonic oblique-wing research aircraft to assess the effects of compressibility, evaluate a more representative structure, and analyze flight performance at transonic speeds (those on either side of the speed of sound).
The aircraft was delivered to the Dryden Flight Research Center, Edwards, CA, in March 1979 and its first flight was on December 21, 1979. Piloting the aircraft on that flight, as well as on its last flight on August 7, 1982, was NASA Research Pilot Thomas C. McMurtry. The AD-1 flew a total of 79 times during the research program. The aircraft was constructed by the Ames Industrial Co., Bohemia, NY, under a $240,000 fixed-price contract. NASA specified the design based on a geometric configuration provided by the Boeing company. The Rutan Aircraft Factory, Mojave, CA, provided the detailed design and loads analysis for the vehicle.
The aircraft was 38.8 feet long and 6.75 feet high with a wing span of 32.3 feet, unswept. It was constructed of plastic reinforced with fiberglass and weighed 1,450 pounds,empty. The vehicle was powered by two small turbojet engines, each producing 220 pounds of thrust at sea level. Due to safety concerns, the aircraft was limited to speeds of 170 mph.
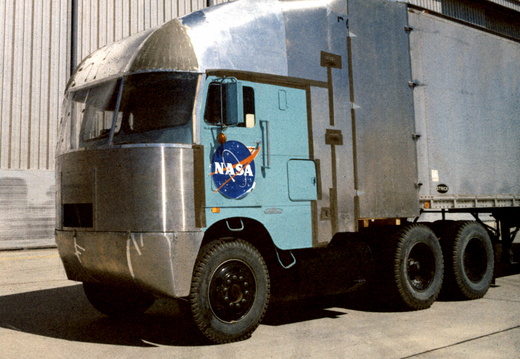
Aerodynamic Truck
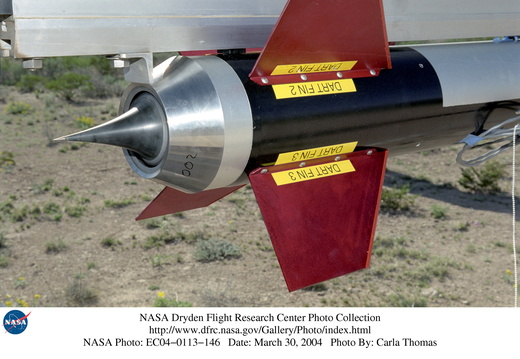
Aerospike Rocket Test
The Dryden Aerospike Rocket Test provided the first known data from a solid-fueled aerospike rocket in flight. The test took place March 30 and 31, 2004, at the King Ranch launch site at the Pecos County Aerospace Development Corporation Flight Test Range in Fort Stockton, Texas.
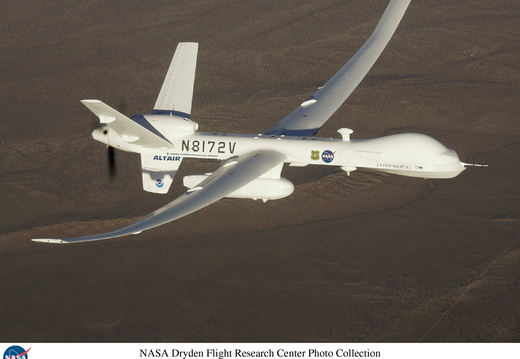
Altair
General Atomics Aeronautical Systems, Inc., is developing the Altair version of its Predator B unmanned reconnaissance aircraft under NASA's Environmental Research Aircraft and Sensor Technology (ERAST) project. NASA plans to use the Altair as a technology demonstrator to validate a variety of command and control technologies for UAVs, as well as demonstrate the capability to perform a variety of Earth science missions.
The Altair is designed to carry an 700-lb. payload of scientific instruments and imaging equipment for as long as 32 hours at up to 52,000 feet altitude. Eleven-foot extensions have been added to each wing, giving the Altair an overall wingspan of 86 feet with an aspect ratio of 23. It is powered by a 700-hp. rear-mounted TPE-331-10 turboprop engine, driving a three-blade propeller. Altair is scheduled to begin flight tests in the fourth quarter of 2002, and be acquired by NASA following successful completion of basic airworthiness tests in early 2003 for evaluation of over-the-horizon control, detect, see and avoid and other technologies required to allow UAVs to operate safely with other aircraft in the national airspace.
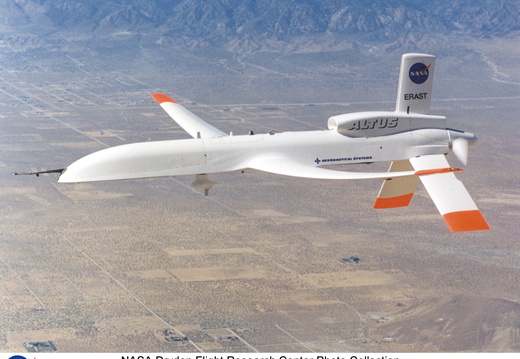
Altus
The Altus I, completed in 1997, flew a series of development flights at Dryden that summer. Those test flights culminated with the craft reaching an altitude of 43,500 ft while carrying a simulated 300-lb payload, a record for an unmanned aircraft powered by a piston engine augmented with a single-stage turbocharger.
The Altus II sustained an altitude of 55,000 feet for four hours in 1999. A pilot in a control station on the ground flies the craft by radio signals, using visual cues from a video camera in the nose of the Altus and information from the craft’s air data system.
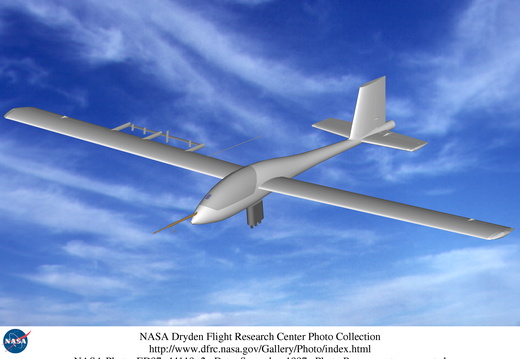
Apex
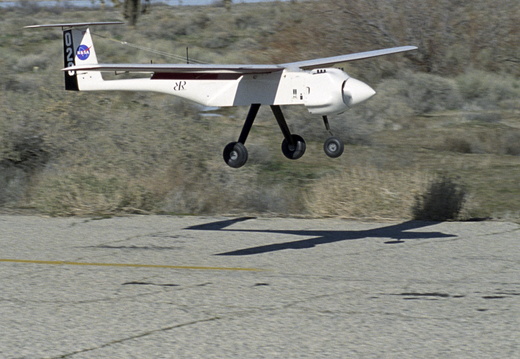
APV-3
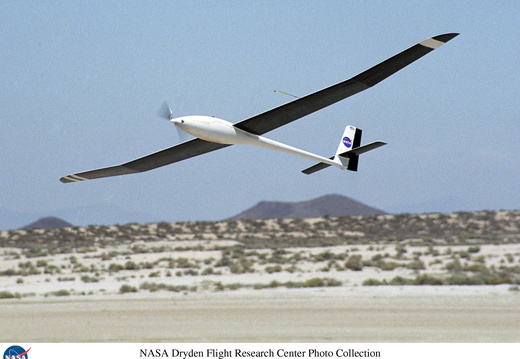
Autonomous Soaring Project
Just as sailplanes use thermal lift and updrafts to soar for extended periods of time, the Autonomous Soaring Project flew a lightweight 15-pound motor-glider to demonstrate that the same concept could be applied to small, powered UAVs to both increase their endurance and save energy.
The remote-controlled model sailplane was modified to incorporate a small electric motor and an autopilot, the latter reprogrammed to detect thermals or updrafts. The software programmed into the autopilot flew the aircraft on a pre-determined racetrack over the northern portion of Rogers Dry Lake at Edwards Air Force Base until it detected an updraft. As the aircraft rose, the engine automatically shut off and the aircraft circled to stay within the convective lift resulting from the thermal or updraft without any human intervention.
A project engineer said the small UAV added 60 minutes to its endurance by soaring autonomously, using thermals that formed over the dry lakebed. Nicknamed Cloud Swift after a bird known for feeding on insects found in rising air masses, the modified model sailplane gained an average altitude of 565 feet in 23 updrafts during 17 flights, and in one strong thermal ascended 2,770 feet.
Small, portable UAVs with long-endurance capabilities could fulfill a number of surveillance roles including forest fire monitoring, traffic control and search and rescue.
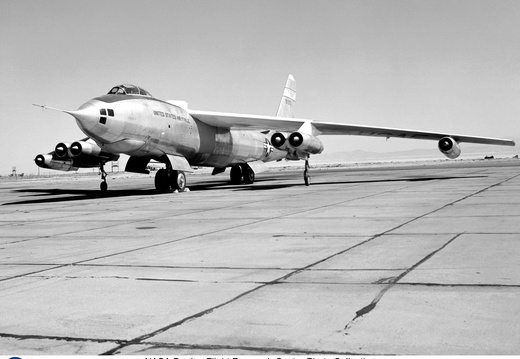
B-47A
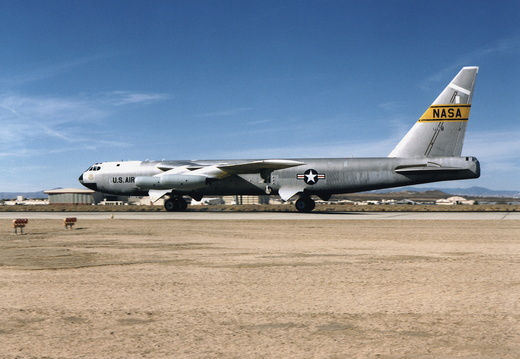
B-52 STRATOFORTRESS
Some of the significant projects supported by B-52 008 included the X-15, the lifting bodies, HiMAT (highly maneuverable aircraft technology), Pegasus, validation of parachute systems developed for the space shuttle program (solid-rocket-booster recovery system and the orbiter drag chute system), and the X-38.
The B-52 served as the launch vehicle on 106 X-15 flights and flew a total of 159 captive-carry and launch missions in support of that program from June 1959 to October 1968. Information gained from the highly successful X-15 program contributed to the Mercury, Gemini, and Apollo human spaceflight programs as well as space shuttle development. Between 1966 and 1975, the B-52 served as the launch aircraft for 127 of the 144 wingless lifting body flights. In the 1970s and 1980s, the B-52 was the launch aircraft for several aircraft at what is now the Dryden Flight Research Center, Edwards, California, to study spin-stall, high-angle-of attack, and maneuvering characteristics. These included the 3/8-scale F-15/spin research vehicle (SRV), the HiMAT (Highly Maneuverable Aircraft Technology) research vehicle, and the DAST (drones for aerodynamic and structural testing). The aircraft supported the development of parachute recovery systems used to recover the space shuttle solid rocket booster casings. It also supported eight orbiter (space shuttle) drag chute tests in 1990. In addition, the B-52 served as the air launch platform for the first six Pegasus space boosters.
During its many years of service, the B-52 underwent several modifications. The first major modification was made by North American Aviation (now part of Boeing) in support of the X-15 program. This involved creating a launch-panel-operator station for monitoring the status of the test vehicle being carried, cutting a large notch in the right inboard wing flap to accommodate the vertical tail of the X-15 aircraft, and installing a wing pylon that enables the B-52 to carry research vehicles and test articles to be air-launched/dropped. Located on the right wing, between the inboard engine pylon and the fuselage, this wing pylon was subjected to extensive testing prior to its use. For each test vehicle the B-52 carried, minor changes were made to the launch-panel operator's station.
Built originally by the Boeing Company, the NASA B-52 was powered by eight Pratt & Whitney J57-19 turbojet engines, each of which produced 12,000 pounds of thrust. The aircraft's normal launch speed was Mach 0.8 (about 530 miles per hour) and its normal drop altitude was 40,000 to 45,000 feet. It was 156 feet long and had a wing span of 185 feet. The heaviest load it carried was the No. 2 X-15 aircraft at 53,100 pounds. Project manager for the aircraft was Roy Bryant.
Another B-52 (an A-model), Tail Number 003, also flew as a mothership, launching the X-15 and lifting bodies.
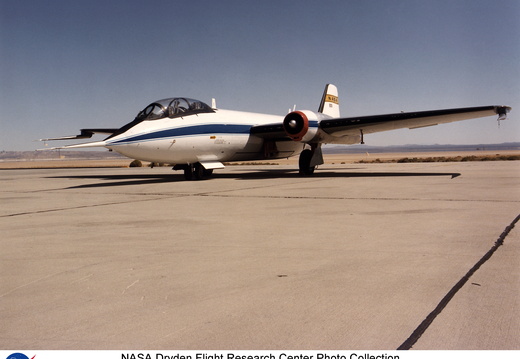
B-57B
The early 1970s showed a growing interest in continuing atmospheric research. The B-57B was at the NASA Flight Research Center for a joint program with NASA Langley Research Center, Hampton, Virginia and was having a special set of instrumentation installed. Delays in completing the instruments provided an opportunity to support the NASA space program. The B-57B was used in proof-of-concept testing of the Viking Mars landers. The deceleration drop testing part of the program took place at the Joint Parachute Test Facility, El Centro, California.
With completion of the Viking parachute tests, the B-57B was flown for measuring and analysis of atmospheric turbulence research in 1974-75 as part of a joint NASA program between the Flight Research Center and Langley Research Center. Additional atmospheric testing provided samples of aerosols for the University of Wyoming and clear-air turbulence data for the Department of Transportation.
The aircraft was tested over a span of many years at Edwards Air Force Base by various NASA centers for other types of research. Earlier, in the 1960s, the aircraft was flown at the Flight Research Center by the Lewis Research Center (now the John Glenn Research Center) in support of the newly established NASA Electronics Center in Boston, Massachusetts. Later, in 1982, the B-57B aircraft returned to the (then) Ames-Dryden Flight Research Facility for more Langley-sponsored turbulence testing.
The atmospheric research conducted using the B-57B Canberra provided information on mountain waves, jet streams, convective turbulence, and clear-air turbulence.
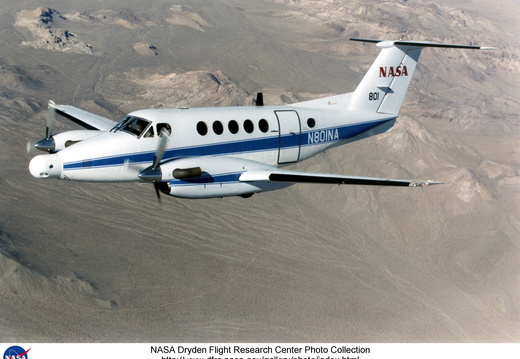
Beechcraft KingAir
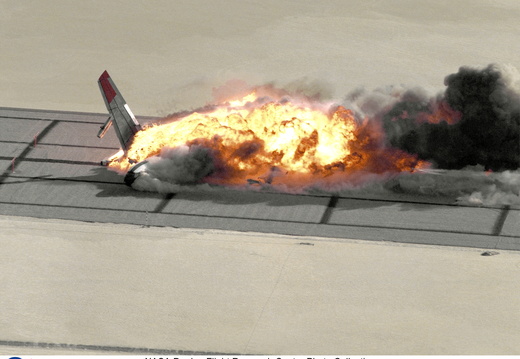
Boeing 720
This anti-misting kerosene (AMK) cannot be introduced directly into a gas turbine engine due to several possible problems such as clogging of filters. The AMK must be restored to almost Jet-A before being introduced into the engine for burning. This restoration is called "degradation" and was accomplished on the B-720 using a device called a "degrader." Each of the four Pratt & Whitney JT3C-7 engines had a "degrader" built and installed by General Electric (GE) to break down and return the AMK to near Jet-A quality.
In addition to the AMK research the NASA Langley Research Center was involved in a structural loads measurement experiment, which included having instrumented dummies filling the seats in the passenger compartment. Before the final flight on December 1, 1984, more than four years of effort passed trying to set-up final impact conditions considered survivable by the FAA. During those years while 14 flights with crews were flown the following major efforts were underway: NASA Dryden developed the remote piloting techniques necessary for the B-720 to fly as a drone aircraft; General Electric installed and tested four degraders (one on each engine); and the FAA refined AMK (blending, testing, and fueling a full-size aircraft). The 15 flights had 15 takeoffs, 14 landings and a larger number of approaches to about 150 feet above the prepared crash site under remote control. These flight were used to introduce AMK one step at a time into some of the fuel tanks and engines while monitoring the performance of the engines. On the final flight (No. 15) with no crew, all fuel tanks were filled with a total of 76,000 pounds of AMK and the remotely-piloted aircraft landed on Rogers Dry Lakebed in an area prepared with posts to test the effectiveness of the AMK in a controlled impact.
The CID, which some wags called the Crash in the Desert, was spectacular with a large fireball enveloping and burning the B-720 aircraft. From the standpoint of AMK the test was a major set-back, but for NASA Langley, the data collected on crashworthiness was deemed successful and just as important.
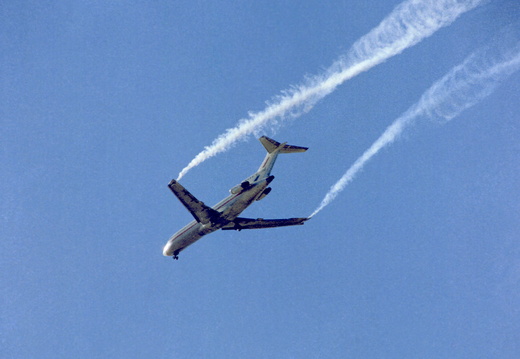
Boeing 727
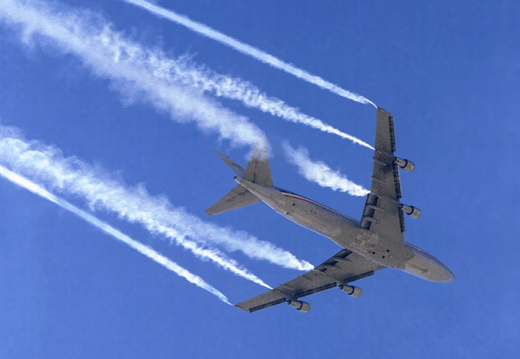
Boeing 747
The data gathered in the 747 studies complemented data from the previous (1973-74) joint NASA Flight Research Center and Federal Aviation Administration (FAA) Boeing 727 wake vortices study.
Six smoke generators were installed under the wings of the 747 to provide a visual image of the trailing vortices. The object of the experiments was to test different configurations and mechanical devices on the747 that could be used to break up or lessen the strength of the vortices. The results of the tests could lead to shorter spacing between landings and takeoffs, which, in turn, could alleviate air-traffic congestion. For approximately 30 flights the 747 was flown using various combinations of wing air spoilers in an attempt to reduce wake vortices. To evaluate the effectiveness of the different configurations, chase aircraft were flown into the vortex sheets to probe their strengths and patterns at different times. Two of the chase planes used were the Flight Research Center’s Cessna T-37 and the NASA Ames Research Center’s Learjet. These aircraft represented the types of smaller business jets and other small aircraft that might encounter large passenger aircraft on approach or landings around major airports or in flight.
Tests without the 747’s wing spoilers deployed produced violent "upset" problems for the T-37 aircraft at a distance of approximately 3 miles. From the magnitude of the problems found, distances of as much as ten miles might be required if spoilers were not used. With two spoilers on the outer wing panels, the T-37 could fly at a distance of three miles and not experience the "upset" problem. The wake vortex study continued even after the 747 was returned to its primary mission of carrying the Space Shuttle.
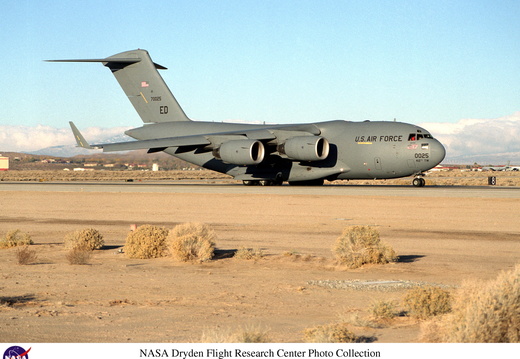
C-17 Globemaster III
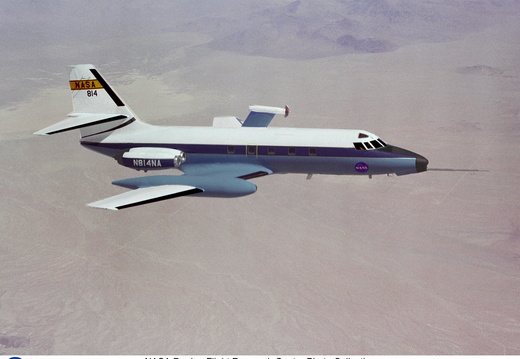
C-140 JetStar
In 1985, the JetStar's wings were modified with suction and spray devices in a laminar (smooth) air flow program to study ways of improving the flow of air over the wings of airliners. The program also studied ways of reducing the collection of ice and insects on airliner wings.
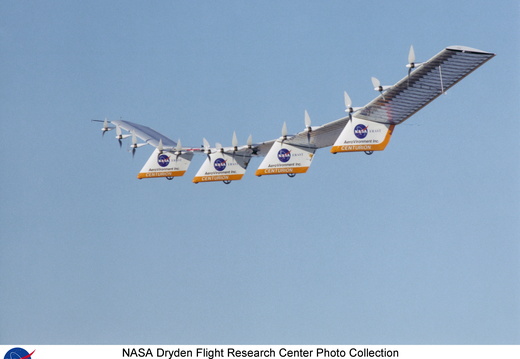
Centurion
The airplane was believed to be the first aircraft designed to achieve sustained horizontal flight at altitudes of 90,000 to 100,000 feet. Achieving this capability would meet the ERAST goal of developing an ultrahigh-altitude airplane that could meet the needs of the science community to perform upper-atmosphere environmental data missions. Much of the technology leading to the Centurion was developed during the Pathfinder and Pathfinder-Plus projects.
However, in the course of its development, the Centurion became a prototype technology demonstration aircraft designed to validate the technology for the Helios, a planned future high-altitude, solar-powered aircraft that could fly for weeks or months at a time on science or telecommunications missions. Centurion had 206-foot-long wings and used batteries to supply power to the craft's 14 electric motors and electronic systems.
Centurion first flew at Dryden Nov. 10, 1998, and followed up with a second test flight Nov. 19. On its third and final flight on Dec. 3, the craft was aloft for 31 minutes and reached an altitude of about 400 feet. All three flights were conducted over a section of Rogers Dry Lake adjacent to Dryden. For its third flight, the Centurion carried a simulated payload of more than 600 pounds--almost half the lightweight aircraft's empty weight. John Del Frate, Dryden's project manager for solar-powered aircraft, said he was impressed to see how well the aircraft handled the large weight increase from an initial payload of 150 pounds to one of 600 pounds.
During 1999, Centurion gave way to the Helios Prototype, the latest and largest example of a slow-flying ultralight flying wing designed for long-duration, high-altitude Earth science or telecommunications relay missions. This was an enlarged version of the Centurion flying wing with a wingspan of 247 feet, 41 feet greater than the Centurion, 2 1/2 times that of the solar-powered Pathfinder flying wing, and longer than the wingspans of either the Boeing 747 jetliner or Lockheed C-5 transport aircraft. In upgrading the Centurion to the Helios Prototype configuration, AeroVironment added a sixth wing section and a fifth landing gear pod, among other improvements. The additional wingspan increased the area available for installation of solar cells and improved its lifting capability. This allows the Helios Prototype to carry a regenerative fuel-cell-based energy storage system that will enable flight at night, while still meeting the performance goals originally established for the Centurion.
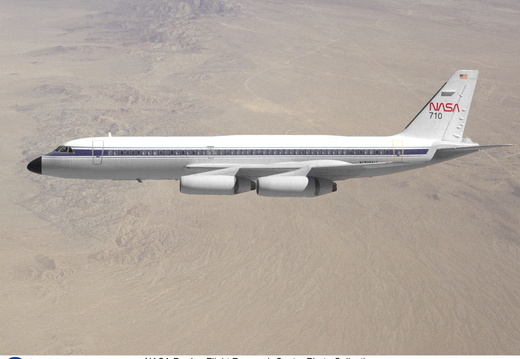
CV-990 LSRA
The TAV was built from a kit and modified into a radio controlled, video-equipped machine to drill holes in aircraft test tires that were in imminent danger of exploding because of one or more conditions: high air pressure, high temperatures, and cord wear.
An exploding test tire releases energy equivalent to two and one-half sticks of dynamite and can cause severe injuries to anyone within 50 ft. of the explosion, as well as ear injury - possibly permanent hearing loss - to anyone within 100 ft. The degree of danger is also determined by the temperature pressure and cord wear of a test tire.
The TAV was developed by David Carrott, a PRC employee under contract to NASA.
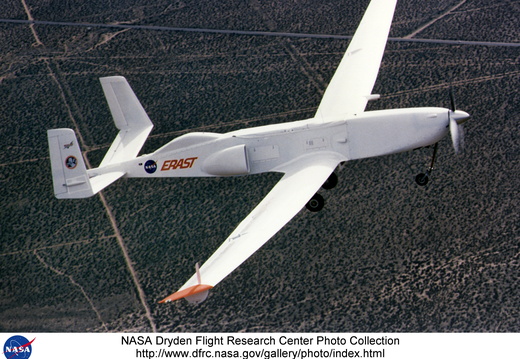
D-2
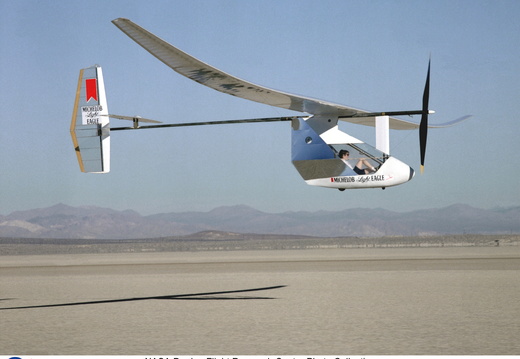
Daedalus
To celebrate the Greek myth of Daedalus, the man who constructed wings of wax and feathers to escape King Minos, the Daedalus project began with the goal of designing, building and testing a human-powered aircraft that could fly the mythical distance, 115 km. To achieve this goal, three aircraft were constructed. The Light Eagle was the prototype aircraft, weighing 92 pounds. On January 22, 1987, it set a closed course distance record of 59 km, which still stands. Also in January of 1987, the Light Eagle was powered by Lois McCallin to set the straight distance, the distance around a closed circuit, and the duration world records for the female division in human powered vehicles.
Following this success, two more aircraft were built, the Daedalus 87 and Daedalus 88. Each aircraft weighed approximately 69 pounds. The Daedalus 88 aircraft was the ship that flew the 199 km from the Iraklion Air Force Base on Crete in the Mediterranean Sea, to the island of Santorini in 3 hours, 54 minutes. In the process, the aircraft set new records in distance and endurance for a human powered aircraft.
The specific areas of flight research conducted at Dryden included characterizing the rigid body and flexible dynamics of the Light Eagle, investigating sensors for an autopilot that could be used on high altitude or human powered aircraft, and determining the power required to fly the Daedalus aircraft.
The research flights began in late December 1987 with a shake-down of the Light Eagle instrumentation and data transfer links. The first flight of the Daedalus 87 also occurred during this time. On February 7, 1988, the Daedalus 87 aircraft crashed on Rogers Dry Lakebed. The Daedalus 88, which later set the world record, was then shipped from MIT to replace the 87's research flights, and for general checkout procedures. Due to the accident, flight testing was extended four weeks and thus ended in mid-March 1988 after having achieved the major goals of the program; exploring the dynamics of low Reynolds number aircraft, and investigating the aeroelastic behavior of lightweight aircraft. The information obtained from this program had direct applications to the later design of many high-altitude, long endurance aircraft.
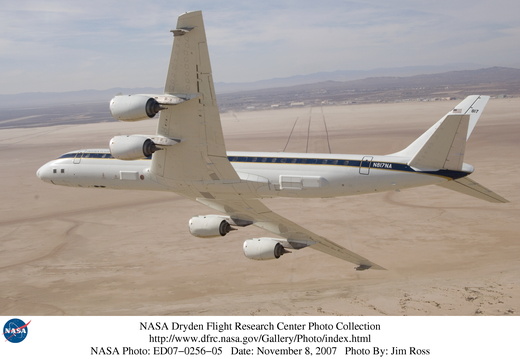
DC-8
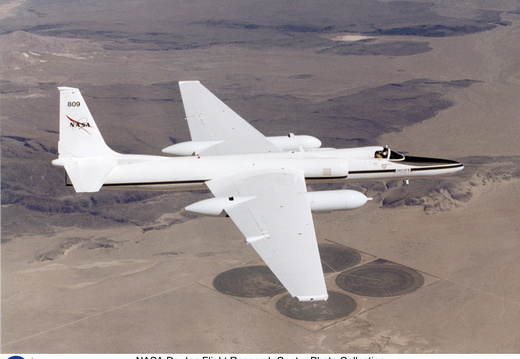
ER-2
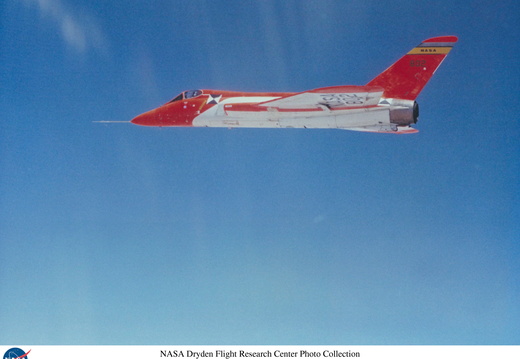
F-5D
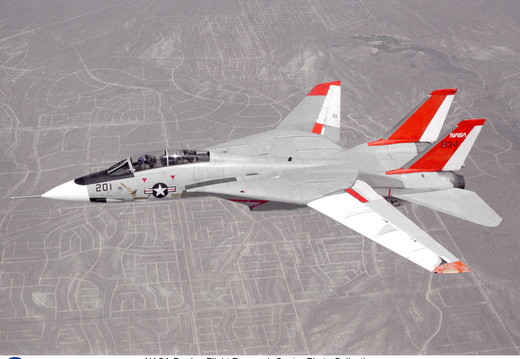
F-14 TOMCAT
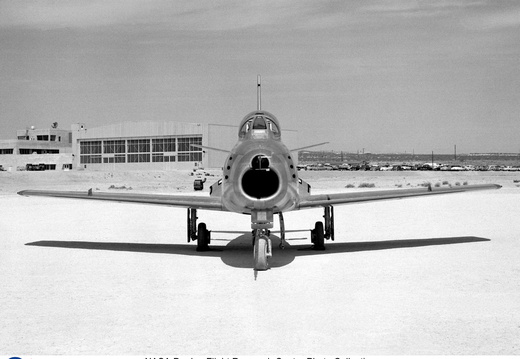
F-86
The F-86 had a 35 degree sweptwing and a wing span of 37 feet 1 inch with a General Electric J47-GE engine. It was the first U.S. sweptwing fighter and saw extensive action in the Korean War. It could slightly exceed Mach 1 in a dive.
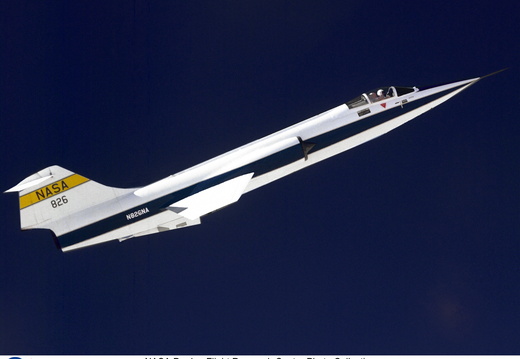
F-104
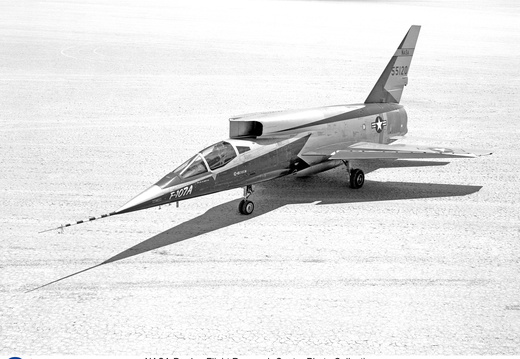
F-107A
The third aircraft built, F-107A (Serial #55-5120) made its first NACA flight on July 25, 1958. It would complete 39 more flights during 1958 and 1959 before being damaged in a takeoff accident on September 1, 1959, fortunately without injury to the pilot.
During this period a sidestick program was NACA's major accomplishment with the craft, after the proposed inlet and fin studies went by the wayside. The complex inlet, with its movable inlet ramps and variable inlet control, caused many problems and was finally positioned in a fixed mode. Engineers at NACA modified the F-107A NACA #120, with a so-called Sidestick Flight Control System. (Sidestick was the center stick, modified and moved to the side of the cockpit area and could be used with wrist motion only) This system had been planned for the upcoming X-15 program. North American refined the design and the designated X-15 test pilots gained experience before having to use it in the actual X-15 airplane.
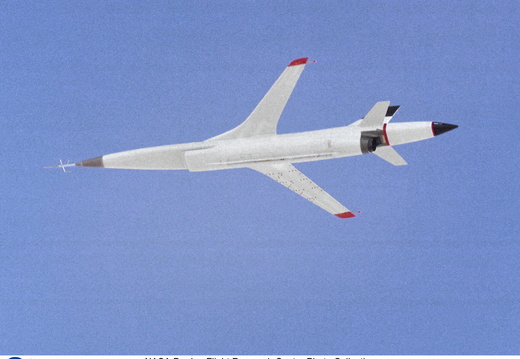
Firebee Drone - DAST
From 1977 to 1983, the Dryden Flight Research Center, Edwards, California, (under two different names) conducted the DAST Program as a high-risk flight experiment using a ground-controlled, pilotless aircraft. Described by NASA engineers as a "wind tunnel in the sky," the DAST was a specially modified Teledyne-Ryan BQM-34E/F Firebee II supersonic target drone that was flown to validate theoretical predictions under actual flight conditions in a joint project with the Langley Research Center, Hampton, Virginia.
The DAST Program merged advances in electronic remote control systems with advances in airplane design. Drones (remotely controlled, missile-like vehicles initially developed to serve as gunnery targets) had been deployed successfully during the Vietnamese conflict as reconnaissance aircraft. After the war, the energy crisis of the 1970s led NASA to seek new ways to cut fuel use and improve airplane efficiency. The DAST Program's drones provided an economical, fuel-conscious method for conducting in-flight experiments from a remote ground site. DAST explored the technology required to build wing structures with less than normal stiffness. This was done because stiffness requires structural weight but ensures freedom from flutter-an uncontrolled, divergent oscillation of the structure, driven by aerodynamic forces and resulting in structural failure. The program used refined theoretical tools to predict at what speed flutter would occur. It then designed a high-response control system to counteract the motion and permit a much lighter wing structure. The wing had, in effect, "electronic stiffness."
Flight research with this concept was extremely hazardous because an error in either the flutter prediction or control system implementation would result in wing structural failure and the loss of the vehicle. Because of this, flight demonstration of a sub-scale vehicle made sense from the standpoint of both safety and cost. The program anticipated structural failure during the course of the flight research.
The Firebee II was a supersonic drone selected as the DAST testbed because its wing could be easily replaced, it used only tail-mounted control surfaces, and it was available as surplus from the U. S. Air Force. It was capable of 5-g turns (that is, turns producing acceleration equal to 5 times that of gravity). Langley outfitted a drone with an aeroelastic, supercritical research wing suitable for a Mach 0.98 cruise transport with a predicted flutter speed of Mach 0.95 at an altitude of 25,000 feet.
Dryden and Langley, in conjunction with Boeing, designed and fabricated a digital flutter suppression system (FSS). Dryden developed an RPRV (remotely piloted research vehicle) flight control system; integrated the wing, FSS, and vehicle systems; and conducted the flight program. In addition to a digital flight control system and aeroelastic wings, each DAST drone had research equipment mounted in its nose and a mid-air retrieval system in its tail. The drones were originally launched from the NASA B-52 bomber and later from a DC-130. The DAST vehicle's flight was monitored from the sky by an F-104 chase plane.
When the DAST's mission ended, it deployed a parachute and then a specially equipped Air Force helicopter recovered the drone in mid-air. On the ground, a pilot controlled the DAST vehicle from a remote cockpit while researchers in another room monitored flight data transmitted via telemetry. They made decisions on the conduct of the flight while the DAST was in the air. In case of failure in any of the ground systems, the DAST vehicle could also be flown to a recovery site using a backup control system in the F-104.
The DAST Program experienced numerous problems. Only eighteen flights were achieved, eight of them captive (in which the aircraft flew only while still attached to the launch aircraft). Four of the flights were aborted and two resulted in crashes--one on June 12, 1980, and the second on June 1, 1983. Meanwhile, flight experiments with higher profiles, better funded remotely piloted research vehicles took priority over DAST missions. After the 1983 crash, which was caused by a malfunction that disconnected the landing parachute from the drone, the program was disbanded.
Because DAST drones were considered expendable, certain losses were anticipated. Managers and researchers involved in other high-risk flight projects gained insights from the DAST program that could be applied to their own flight research programs. The DAST aircraft had a wingspan of 14 feet, four inches and a nose-to-tail length of 28 feet, 4 inches. The fuselage had a radius of about 2.07 feet. The aircraft's maximum loaded weight was about 2,200 pounds. It derived its power from a Continental YJ69-T-406 engine.
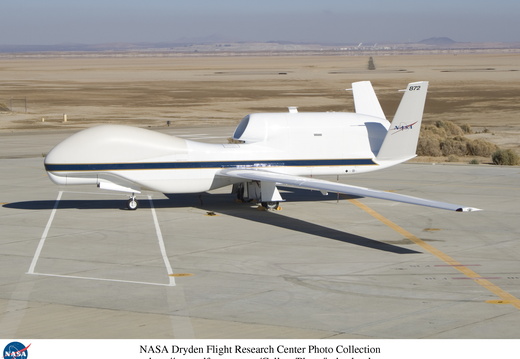
Global Hawk
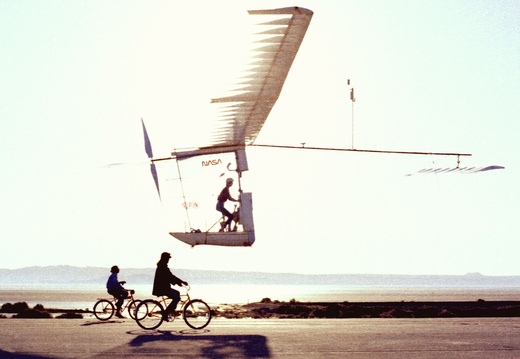
Gossamer Albatross
The first flight of a solar-powered aircraft took place on November 4, 1974, when the remotely controlled Sunrise II, designed by Robert J. Boucher of AstroFlight, Inc., flew following a launch from a catapult.
Following this event, AeroVironment, Inc. (founded in 1971 by the ultra-light airplane innovator--Dr. Paul MacCready) took on a more ambitious project to design a human-piloted, solar-powered aircraft. The firm initially took the human-powered Gossamer Albatross II and scaled it down to three-quarters of its previous size for solar-powered flight with a human pilot controlling it. This was more easily done because in early 1980 the Gossamer Albatross had participated in a flight research program at NASA Dryden in a program conducted jointly by the Langley and Dryden research centers. Some of the flights were conducted using a small electric motor for power.
Gossamer Penguin
The scaled-down aircraft was designated the Gossamer Penguin. It had a 71-foot wingspan compared with the 96-foot span of the Gossamer Albatross. Weighing only 68 pounds without a pilot, it had a low power requirement and thus was an excellent test bed for solar power.
AstroFlight, Inc., of Venice, Calif., provided the power plant for the Gossamer Penguin, an Astro-40 electric motor. Robert Boucher, designer of the Sunrise II, served as a key consultant for both this aircraft and the Solar Challenger. The power source for the initial flights of the Gossamer Penguin consisted of 28 nickel-cadmium batteries, replaced for the solar-powered flights by a panel of 3,920 solar cells capable of producing 541 Watts of power.
The battery-powered flights took place at Shafter Airport near Bakersfield, Calif. Dr. Paul MacCready’s son Marshall, who was 13 years old and weighed roughly 80 pounds, served as the initial pilot for these flights to determine the power required to fly the airplane, optimize the airframe/propulsion system, and train the pilot. He made the first flights on April 7, 1980, and made a brief solar-powered flight on May 18.
The official project pilot was Janice Brown, a Bakersfield school teacher who weighed in at slightly under 100 pounds and was a charter pilot with commercial, instrument, and glider ratings. She checked out in the plane at Shafter and made about 40 flights under battery and solar power there. Wind direction, turbulence, convection, temperature and radiation at Shafter in mid-summer proved to be less than ideal for Gossamer Penguin because takeoffs required no crosswind and increases in temperature reduced the power output from the solar cells.
Consequently, the project moved to Dryden in late July, although conditions there also were not ideal. Nevertheless, Janice finished the testing, and on August 7, 1980, she flew a public demonstration of the aircraft at Dryden in which it went roughly 1.95 miles in 14 minutes and 21 seconds.
This was significant as the first sustained flight of an aircraft relying solely on direct solar power rather than batteries. It provided the designers with practical experience for developing a more advanced, solar-powered aircraft, since the Gossamer Penguin was fragile and had limited controllability. This necessitated its flying early in the day when there were minimal wind and turbulence levels, but the angle of the sun was also low, requiring a panel for the solar cells that could be tilted toward the sun.
Using the specific conclusions derived from their experience with Gossamer Penguin, the AeroVironment engineers designed Solar Challenger, a piloted, solar-powered aircraft strong enough to handle both long and high flights when encountering normal turbulence.
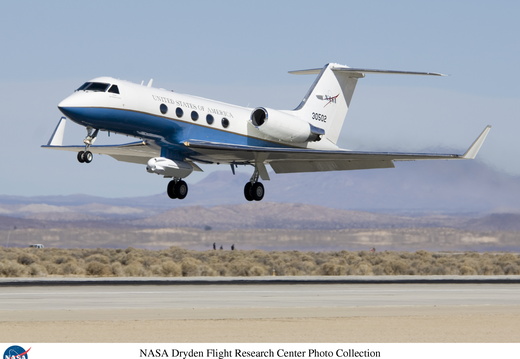
Gulfstream III
As a Multi-Role Cooperative Research Platform, the heavily instrumented twin-turbofan aircraft provides long-term capability for efficient testing of subsonic flight experiments for NASA, the U.S. Air Force, other government agencies, academia, and private industry. Originally designated a C-20A by the Air Force, the aircraft was declared excess by that service and transferred to NASA Dryden at Edwards AFB, Calif., in September 2002.
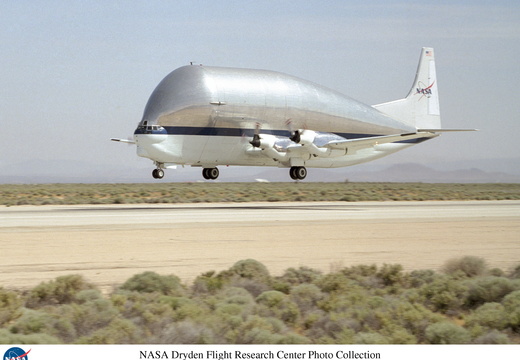
Guppy
The various Guppies were modified from 1940's and 50's-vintage Boeing Model 377 and C-97 Stratocruiser airframes by Aero Spacelines, Inc., which operated the aircraft for NASA. NASA's Flight Research Center assisted in certification testing of the first Pregnant Guppy in 1962. One of the turboprop-powered Super Guppies, built up from a YC-97J airframe, last appeared at Dryden in May, 1976 when it was used to transport the HL-10 and X-24B lifting bodies from Dryden to the Air Force Museum at Wright-Patterson Air Force Base, Ohio.
NASA's present Super Guppy Turbine, the fourth and last example of the final version, first flew in its outsized form in 1980. It and its three sister ships were built in the 1970s for Europe's Airbus Industrie to ferry outsized structures for Airbus jetliners to the final assembly plant in Toulouse, France. It later was acquired by the European Space Agency, and then acquired by NASA
in late 1997 for transport of large structures for the International Space Station to the launch site. It replaced the earlier-model Super Guppy, which has been retired and is used for spare parts. NASA's Super Guppy Turbine carries NASA registration number N941NA, and is based at Ellington Field near the Johnson Space Center.
For more information on NASA's Super Guppy Turbine, log onto the Johnson Space Center Super Guppy web page at http://spaceflight.nasa.gov/station/assembly/superguppy/
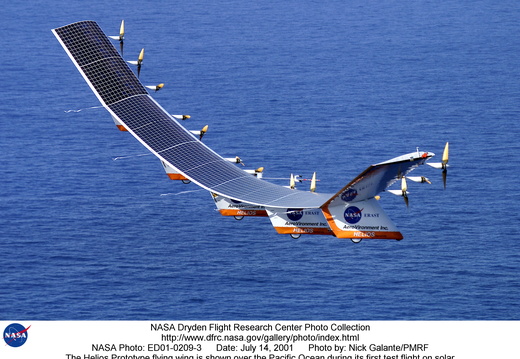
Helios
The Helios Prototype is the latest and largest example of a slow-flying ultralight flying wing designed for high-altitude, long-duration Earth science or telecommunications relay missions. A follow-on to the Pathfinder and Pathfinder-Plus solar aircraft, the Helios Prototype soared to 96,863 feet altitude in August 2001, setting a new world record for sustained altitude by winged aircraft, powered only by energy from the sun.
Developed by AeroVironment, Inc., of Monrovia, Calif., under NASA's Environmental Research Aircraft and Sensor Technology (ERAST) project, the unique craft was designed to demonstrate two key missions: the ability to reach and sustain horizontal flight near 100,000 feet altitude on a single-day flight, and to maintain flight above 50,000 feet altitude for almost two days, the latter mission with the aid of an experimental fuel cell-based supplemental electrical system now in development.
The Helios Prototype is an enlarged version of the Centurion flying wing that flew a series of test flights at Dryden in late 1998. The craft has a wingspan of 247 feet, 41 feet greater than the Centurion, 2 1/2 times that of the Pathfinder flying wing, and longer than the wingspans of either the Boeing 747 jetliner or Lockheed C-5 transport aircraft.
The remotely piloted Helios Prototype first flew during a series of low-altitude checkout and development flights on battery power in late 1999 over Rogers Dry Lake adjacent to NASA's Dryden Flight Research Center in the Southern California desert.
In upgrading the Centurion to the Helios Prototype configuration, AeroVironment added a sixth wing section, a fifth landing gear pod and a differential Global Positioning Satellite (GPS) system to improve navigation, among other improvements. The additional wingspan increased the area available for installation of solar cells and improved aerodynamic efficiency, allowing the Helios Prototype to fly higher, longer and with a larger payload than the smaller craft.
During 2000, more than 62,000 bi-facial silicon solar cells were mounted on the upper surface of Helios' wing. Produced by SunPower, Inc., these solar arrays convert about 19 percent of the solar energy they receive into electrical current and can produce up to 35 kw at high noon on a summer day.
The second milestone established by NASA for its development a long-endurance demonstration flight of almost two days and nights required development of a supplemental electrical power system to provide power at night when the solar arrays are unable to produce electricity. AeroVironment developed an experimental fuel cell-based electrical energy system combining advanced automotive fuel cell components with proprietary control technology designed for the harsh environment above 50,000 feet altitude.
The first version of this system combines gaseous hydrogen from two pressurized tanks mounted on Helios' outboard wing sections with compressed oxygen from the atmosphere via a series of proton-exchange membrane fuel cell "stacks" mounted in the central landing gear pod. The system produces more than 15 kW of direct-current electricity to power Helios' motors and operating systems, with the only by-product being water vapor and heat. The system will increase the Helios Prototype's flight weight by about 800 lb to about 2,400 lb.
Two other versions of the system are contemplated: One, employing liquid hydrogen, would enable the Helios to fly for up to two weeks in the stratosphere anywhere around the Earth, not limited to temperate or equatorial latitudes. Another version, a closed or "regenerative" system, uses water, a fuel cell, and an electrolyzer to form a system similar in function to a rechargeable or "secondary" battery, but with much greater efficiency than the best rechargeable battery systems.
A production version of the Helios with the regenerative fuel cell system is of interest to NASA for environmental science, the military and AeroVironment for various roles, primarily as a stratospheric telecommunications relay platform. With other system reliability improvements, production versions of the Helios are expected to fly missions lasting months at a time, becoming true "atmospheric satellites."
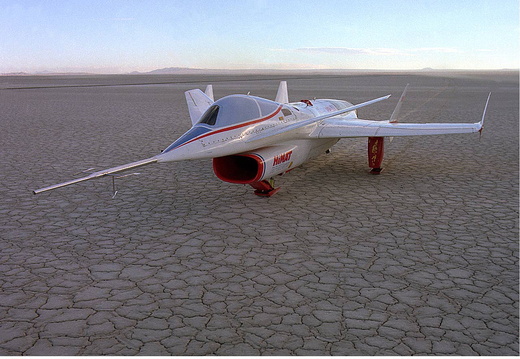
HiMAT
About one-half the size of a standard manned fighter and powered by a small jet engine, the HiMAT vehicles were launched from NASA's B-52 carrier aircraft at an altitude of about 45,000 feet. They were flown remotely by a NASA research pilot from a ground station with the aid of a television camera mounted in the HiMAT cockpits.
Technologies tested on the HiMAT vehicles appearing later on other aircraft include the extensive use of composites common now on military and commercial aircraft; rear-mounted wing and forward canard configuration used very successfully on the X-29 research aircraft flown at Dryden; and winglets, now used on many private and commercial aircraft to lessen wingtip drag and enhance fuel savings.
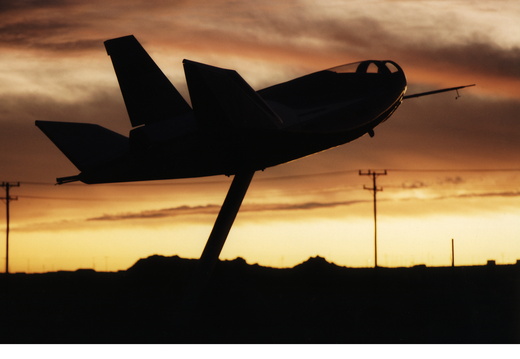
HL-10
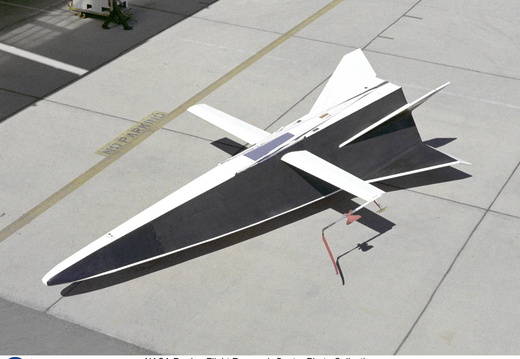
Hyper III
The Hyper III as originally conceived was a stiletto-shaped lifting body that had resulted from a study at NASA’s Langley Research Center in Hampton, Virginia. It was one of a number of hypersonic, cross-range reentry vehicles studied at Langley. (Hypersonic means Mach 5--five times the speed of sound--or faster; cross-range means able to fly a considerable distance to the left or right of the initial reentry path.) The FRC added a small, deployable, skewed wing to compensate for the shape’s extremely low glide ratio. Shop personnel built the 32-foot-long Hyper III and covered its tubular frame with dacron, aluminum, and fiberglass, for about $6,500.
Hyper III employed the same "8-ball" attitude indicator developed for control-room use when flying the X-15, two model-airplane receivers to command the vehicle’s hydraulic controls, and a telemetry system (surplus from the X-15 program) to transmit 12 channels of data to the ground not only for display and control but for data analysis. Dropped from a helicopter at 10,000 feet, Hyper III flew under the control of research pilot Milt Thompson to a near landing using instruments for control. When the vehicle was close to the ground, he handed the vehicle off to experienced model pilot Dick Fischer for a visual landing using standard controls. The flight demonstrated the feasibility of remotely piloting research vehicles and, among other things, that control of the vehicle in roll was much better than predicted and that the vehicle had a much lower lift-to-drag ratio than predicted (a maximum of 4.0 rather than 5.0).
Pilot Milt Thompson exhibited some suprising reactions during the Hyper III flight; he behaved as if he were in the cockpit of an actual research aircraft.
"I was really stimulated emotionally and physically in exactly the same manner that I have been during actual first flights." "Flying the Hyper III from a ground cockpit was just as dramatic as an actual flight in any of the other vehicles....responsibility rather than fear of personal safety is the real emotional driver. I have never come out of a simulator emotionally and physically tired as is often the case after a test flight in a research aircraft. I was emotionally and physically tired after a 3-minute flight of the Hyper III."
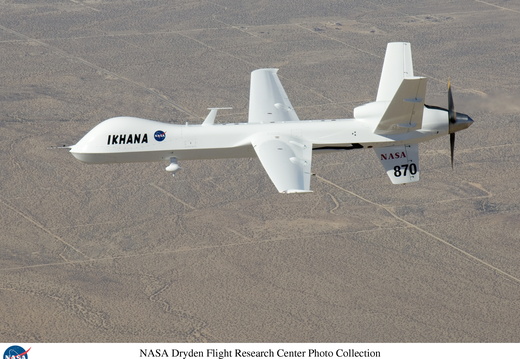
IKHANA
Designed for long-endurance, high-altitude flight, Ikhana will be flown primarily on Earth science missions under the Earth Science Capability Demonstrations project at NASA Dryden. It will also be used for advanced aircraft systems research and technology development.
As part of the Ikhana/Predator B acquisition, NASA also purchased a ground control station and satellite communication system for control of the aircraft and transmittal of research data. The ground control station is in a mobile trailer and, in addition to the pilot's "cockpit," includes computer workstations for scientists and engineers. All of the aircraft systems are mobile, making Ikhana ideal for remote studies.
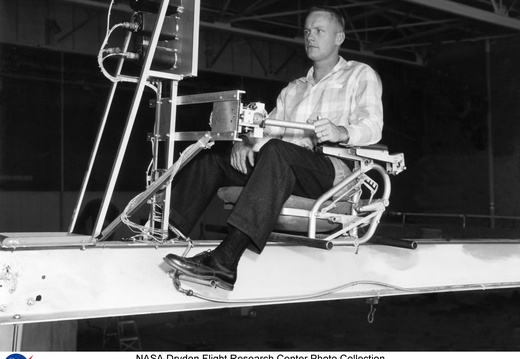
Iron Cross Attitude Simulator
The pioneering jet reaction (reaction control) simulation work at NACA High-Speed Flight Station, spanned the last years of the NACA organization and first NASA years (mid-to-late 1950s.) A two-phase study was begun; one was a fixed-base setup with an analog computer to solve the equations of motion and the other used a three-degree-of freedom mechanical simulator wherein the pilot experienced motions.
The analog computer simulator represented the airplane in five-degrees-of-freedom with control provided from the pilot's short control stick. The stick was unconventional for its time because it was necessary for the pilot to control about three axes through one control device. The stick pivoted fore, aft, and laterally for pitch and roll control, and lateral thumb movement provided yaw control. For most of the study, the pilot presentation consisted of an oscilloscope trace for pitch and bank angle, and a simple volt meter for angle of sideslip.
The Bell X-1B airplane offered an ideal testbed in 1957 for a trial reaction control installation. In preparation, NACA High-Speed Flight Station technicians built an iron-frame simulator, dubbed the "Iron Cross," which matched the dimensions and inertial characteristics of the X-1B, installing small reaction control thrusters on it and then mounting it on a universal joint so that a test pilot could maneuver it in pitch, roll, and yaw. The universal joint from a truck permitted motion about the three axes. High-pressure nitrogen gas was expanded selectively through the six jet nozzles to provide the reaction forces. Flight-type recorders were used to record control stick position and the various angular rates.
NACA's test pilots "flew" this mechanical ground-based simulator extensively.
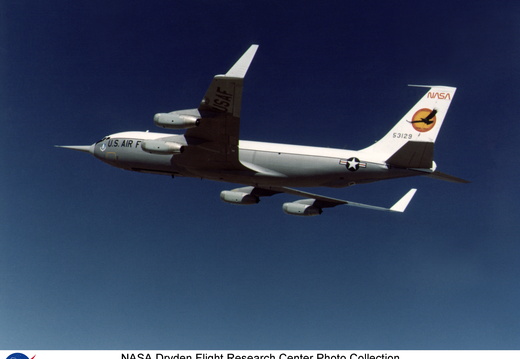
KC-135 STRATOTANKER
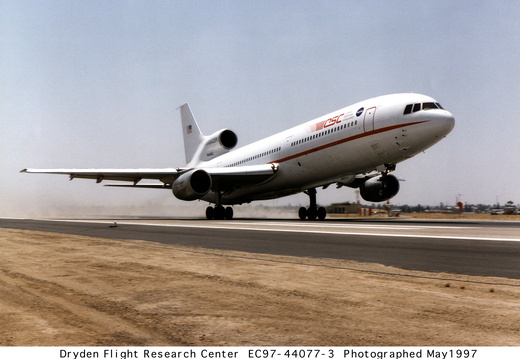
L-1011
The Adaptive Performance Optimization project was designed to reduce the aerodynamic drag of large subsonic transport aircraft by varying the camber of the wing through real-time adjustment of flaps or ailerons in response to changing flight conditions. Reducing the drag will improve aircraft efficiency and performance, resulting in signifigant fuel savings for the nation's airlines worth hundreds of millions of dollars annually.
Flights for the NASA experiment were made over several years on the modified wide-bodied jetliner, with all flights flown out of Bakersfield's Meadows Field. The experiment is part of Dryden's Advanced Subsonic Transport Aircraft Research program.
Dryden conducted extensive wake vortice tests beginning in the 1970's. These wake vortices first became a serious concern when large jetliners were first introduced. The aircraft trailed vortices, created by any large-bodied aircraft, were powerful enough to cause problems for business jets and even other airliners.
Dryden became interested in vortex research both for safety and as a matter of aerodynamics. A wingtip vortex seriously reduces effiecency, causing drag, and therefore a consequent penalty in fuel consumption and performance.
The majority of the tests were conducted using spoilers on a Boeing 747-100, which NASA had just acquired for the Space Shuttle Approach and Landing (ALT) tests. With the two spoilers on the outer panels of each wing extended, the vortices were greatly reduced and the chase aircraft could safely fly five kilometers behind the large aircraft, compared to 15 kilometers with no spoilers.
Dryden's 747 wake vortex studies clearly indicated that the use of spoilers could reduce the severity of wake vortices. In July, 1977, the center began a brief series of tests on a Lockheed L-1011 Tristar to determine if the spoiler that worked so well on the 747 could be applied to other wide-body aircraft as well.
The test showed that while spoilers on the Tristar could reduce wake vortices, they were not as effective in doing so as the spoilers on the 747. NASA is continuing wake vortex studies to this day. These projects can be expected to improve the operational safety of many future aircraft.
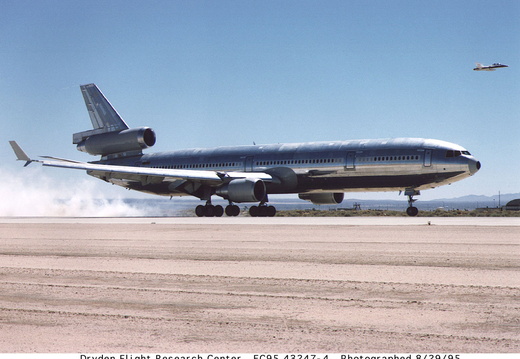
MD-11 Propulsion Controlled Aircraft
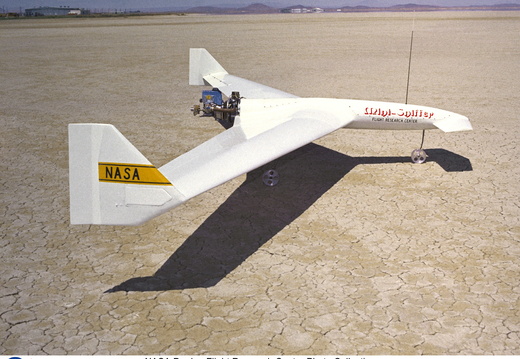
Mini-Sniffer
Three Mini-Sniffer vehicles were built. The number 1 Mini-Sniffer vehicle had swept wings with a span of 18 feet and canards on the nose. It flew 12 flights with the gas-powered engine at low altitudes of around 2,500 feet. The number 1 vehicle was then modified into version number 2 by removing the canards and wing rudders and adding wing tips and tail booms. Twenty flights were made with this version, up to altitudes of 20,000 feet. The number 3 vehicle had a longer fuselage, was lighter in weight, and was powered by the non-air-breathing hydrazine engine designed by NASA's Johnson Space Center in Houston, Texas. This version was designed to fly a 25-pound payload to an altitude of 70,000 feet for one hour or to climb to 90,000 feet and glide back. The number 3 Mini-Sniffer made one flight to 20,000 feet and was not flown again because of a hydrazine leak problem. All three versions used a pusher propeller to free the nose area for an atmospheric-sampling payload.
At various times the Mini-Sniffer has been considered for exploration in the carbon dioxide atmosphere of the planet Mars, where the gravity (38 percent of that on Earth) would reduce the horsepower needed for flight.
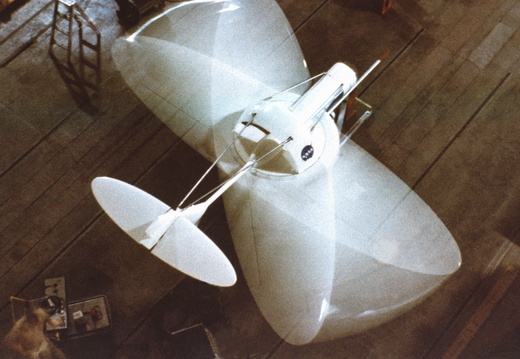
Oblique Wing Research Aircraft
The aircraft's wing was capable of being skewed up to 45 degrees left wing forward. The aircraft was flown in two configurations, the short and long tail version. To aid in the remote piloting task, a television camera was mounted in the nose of the vehicle to provide forward looking views. Power was provided by a 90-horsepower, four cylinder, air-cooled, reciprocating engine.
The flight program was limited to three flights flown over Rosamond dry lakebed at Edwards Air Force Base, of approximately 1 hour each. After the first flight, longitudinal stability problems required a configuration change. The tail was moved back three feet and this configuration was used for the last two flights. Maneuvers were performed at wing skew angles of 0 to 45 degrees. This program provided information which led to flight testing a piloted aircraft with an oblique wing, called the AD-1.
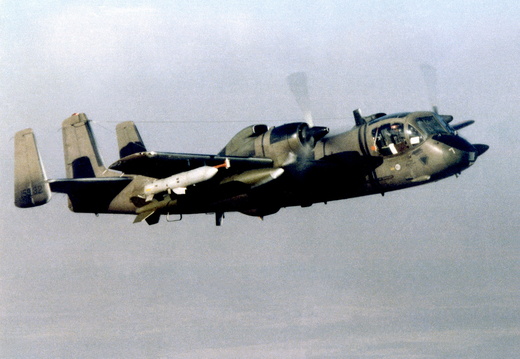
OV-1C
The Mohawk was developed by Grumman Aircraft as a photo observation and reconnaissance aircraft for the US Marines and the US Army. The OV-1 entered production in October 1959 and served the US Army in Europe, Korea, the Viet Nam War, Central and South America, Alaska, and during Desert Shield/Desert Storm in the Middle East. The Mohawk was retired from service in September 1996. 133 OV-1Cs were built, the "C" designating the model which used an IR (infrared) imaging system to provide reconnaissance.
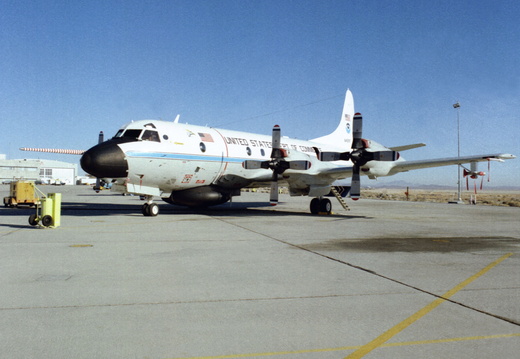
P-3D Orion
Sections of the Space Shuttle thermal protection system’s 6- by 6-inch tiles were mounted on a pylon under the right wing of the WP-3D aircraft. The aircraft was equipped with raindropsize-measuring instruments and cloud radars. The WP-3D weather research aircraft obtained rain impact data for airspeeds between 180 and 260 knots indicated airspeed. Test samples were mounted on two movable doors contained within the left and right sides of the test fixture (for a total of four doors). The doors could be opened or closed to the free-stream airflow during flight at angles of 0, 15, 30, 45, and 60 degrees.
The WP-3D tile testing concentrated on observing the effects of larger drops of moisture at lower speeds. The principle investigator for the tile tests was Robert R. Meyer, Jr., NASA engineer, Ames-Dryden Flight Research Facility.
The Department of Commerce WP-3D aircraft was based at the Miami International Airport. It served as an environmental research platform for oceanographic and atmospheric studies by various government agencies and universities. The WP-3D flown in the Shuttle tile tests was specially instrumented for scientific observation with three radars and an onboard data recording capability. The pylon used for the tile tests could be configured so that specialized equipment could be installed for different users in the scientific community.
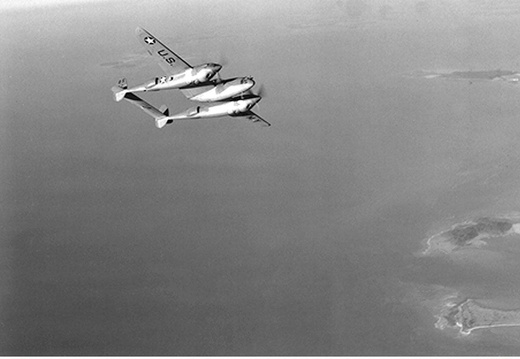
P-38 Lightning
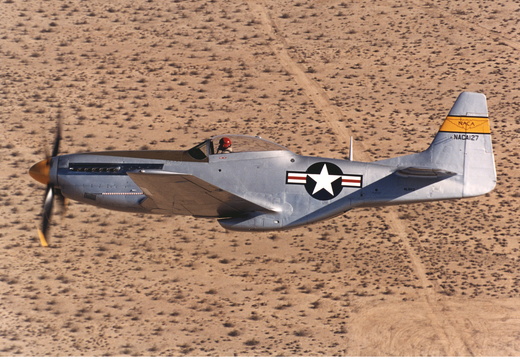
P-51D
The NACA was the National Advisory Committee for Aeronautics, a predecessor of the National Aeronautics and Space Administration (NASA). The HSFRS was a predecessor of NASA’s Dryden Flight Research Center, and Langley Aeronautical Laboratory became NASA’s Langley Research Center.
The P-51D was the first aircraft to employ the NACA laminar-flow airfoil design and could dive to a speed of roughly Mach 0.8. As an F-51 Fighter, instead of a P-51D pursuit aircraft, the aircraft was used as a proficiency aircraft at HSFRS. Records show that the aircraft was also used as a chase and support aircraft 395 times. Neil Armstrong was among the pilots using it to chase some of the X-planes (that is, provide safety support). The P-51D was retired in 1959 as the result of a taxiing mishap.
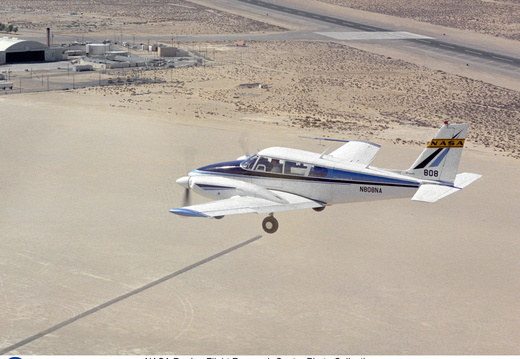
PA-30
A Piper PA-30 Twin Commanche, known as NASA 808, was used at the NASA Dryden Flight Research Center as a rugged workhorse in a variety of research projects associated with both general aviation and military projects.
In the early 1970s, the PA-30, serial number 301498, was used to test a flight technique used to fly Remotely Piloted Research Vehicles (RPRV's). The technique was first tested with the cockpit windows of the light aircraft blacked out while the pilot flew the aircraft utilizing a television monitor which gave him a "pilot's eye" view ahead of the aircraft. Later pilots flew the aircraft from a ground cockpit, a procedure used with all RPRV's. TV and two-way telemetry allow the pilot to be in constant control of the aircraft. The apparatus mounted over the cockpit is a special fish eye lens camera, used to obtain images that are transmitted to the ground based cockpit. This project paved the way for sophisticated, highly successful research programs involving high risk spin, stall, and flight control conditions, such as the HiMAT and the subscale F-15 remotely piloted vehicles.
Over the years, NASA 808 has also been used for spin and stall research related to general aviation aircraft and also research to alleviate wake vortices behind large jetliners.
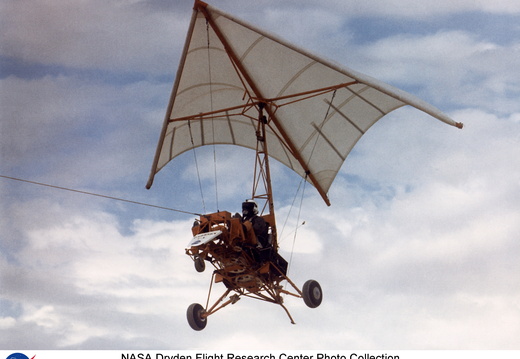
Paresev
The first Paresev flights began with tows across the dry lakebed, in 1962, using a NASA vehicle, a International Harvester carry-all (6 cylinder). Eventually airtows were done using Stearman sport biplane (450 hp), a Piper Super Cub (150-180 hp), Cessna L-19 ( 200 hp Bird Dog) and a Boeing-Vertol HC-1A. Speed range of the Paresev was about 35 - 65 mph.
The Paresev completed nearly 350 flights during a research program from 1962 until 1964. Pilots flying the Paresev included NASA pilots Milton Thompson, Bruce Peterson, and Neil Armstrong from Dryden, Robert Champine from Langley, and Gus Grissom, astronaut. The Paresev was legally transferred to the National Air Museum of the Smithsonian Institute, Washington, D.C.
Despite its looks, the Paresev was a useful research aircraft that helped develop a new way to fly. Although the Rogallo wing was never used on a spacecraft, it revolutionized the sport of hang gliding, and a different but related kind of wing was tested on the X-38 technology demonstrator.
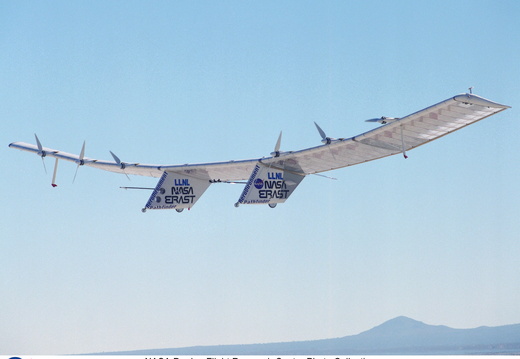
Pathfinder
Solar arrays covered most of the upper wing surface of the Pathfinder aircraft. These arrays provided up to 8,000 watts of power at high noon on a clear summer day. That power fed the aircraft's six electric motors as well as its avionics, communications, and other electrical systems. Pathfinder also had a backup battery system that could provide power for two to five hours, allowing for limited-duration flight after dark.
Pathfinder flew at airspeeds of only 15 to 20 mph. Pitch control was maintained by using tiny elevators on the trailing edge of the wing while turns and yaw control were accomplished by slowing down or speeding up the motors on the outboard sections of the wing. On September 11, 1995, Pathfinder set a new altitude record for solar-powered aircraft of 50,567 feet above Edwards Air Force Base, California, on a 12-hour flight. On July 7, 1997, it set another, unofficial record of 71,500 feet at the Pacific Missile Range Facility, Kauai, Hawaii.
In 1998, Pathfinder was modified into the longer-winged Pathfinder Plus configuration. (See the Pathfinder Plus photos and project description.)
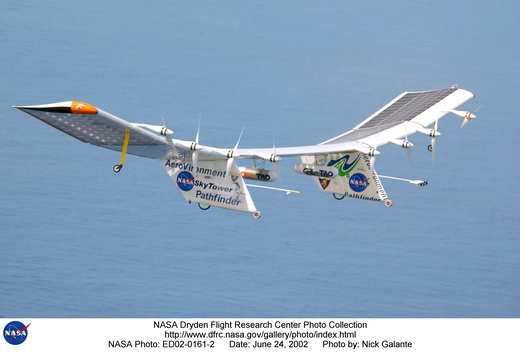
Pathfinder-Plus
The Pathfinder / Pathfinder-Plus is a lightweight, solar-powered, remotely piloted flying wing aircraft that demonstrated the technology of applying solar power for long-duration, high-altitude flight. It was literally the pathfinder for a future fleet of solar-powered aircraft that could stay airborne for weeks or months on scientific sampling and imaging missions.
Solar arrays covering most of the upper wing surface provided power for the aircraft's electric motors, avionics, communications and other electronic systems. Pathfinder also had a backup battery system that could provide power for between two and five hours to allow limited-duration flight after dark.
Pathfinder flew at an airspeed of only 15 to 25 mph. Although pitch control was maintained by the use of tiny elevons on the trailing edge of the wing, turns and yaw control were accomplished by slowing down or speeding up the motors on the outboard sections of the wing.
Pathfinder was designed, built and operated by AeroVironment, Inc., of Monrovia, Calif., the firm that developed the pioneering Gossamer Penguin and Solar Challenger solar-powered aircraft in the late 1970's and early 1980's.
During 1998, the Pathfinder was modified into the extended-wing Pathfinder-Plus configuration. On Aug. 6, 1998, the modified aircraft was flown to a record altitude of 80,201 feet for propeller-driven aircraft. The goal of the flights was to validate new solar, aerodynamic, propulsion and systems technology developed for the Pathfinder's successor, the Helios Prototype, which reached a sustained altitude of almost 97,000 feet in 2001, and other potential solar-powered derivatives in the future.
Essentially a transitional vehicle between the Pathfinder and the follow-on solar aircraft, the Pathfinder-Plus is a hybrid of the technology that was employed on Pathfinder and developed for the Helios.
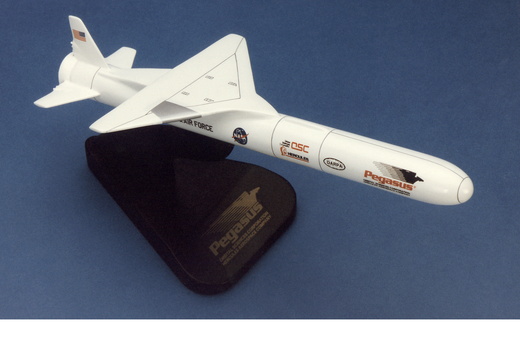
Pegasus
Pegasus is an air-launched space booster produced by Orbital Sciences Corporation and Hercules Aerospace Company (initially; later, Alliant Tech Systems) to provide small satellite users with a cost-effective, flexible, and reliable method for placing payloads into low earth orbit.
Pegasus has been used to launch a number of satellites and the PHYSX experiment. That experiment consisted of a smooth glove installed on the first-stage delta wing of the Pegasus. The glove was used to gather data at speeds of up to Mach 8 and at altitudes approaching 200,000 feet. The flight took place on October 22, 1998.
The PHYSX experiment focused on determining where boundary-layer transition occurs on the glove and on identifying the flow mechanism causing transition over the glove. Data from this flight-research effort included temperature, heat transfer, pressure measurements, airflow, and trajectory reconstruction. Hypersonic flight-research programs are an approach to validate design methods for hypersonic vehicles (those that fly more than five times the speed of sound, or Mach 5).
Dryden Flight Research Center, Edwards, California, provided overall management of the glove experiment, glove design, and buildup. Dryden also was responsible for conducting the flight tests. Langley Research Center, Hampton, Virginia, was responsible for the design of the aerodynamic glove as well as development of sensor and instrumentation systems for the glove. Other participating NASA centers included Ames Research Center, Mountain View, California; Goddard Space Flight Center, Greenbelt, Maryland; and Kennedy Space Center, Florida. Orbital Sciences Corporation, Dulles, Virginia, is the manufacturer of the Pegasus vehicle, while Vandenberg Air Force Base served as a pre-launch assembly facility for the launch that included the PHYSX experiment.
NASA used data from Pegasus launches to obtain considerable data on aerodynamics. By conducting experiments in a piggyback mode on Pegasus, some critical and secondary design and development issues were addressed at hypersonic speeds. The vehicle was also used to develop hypersonic flight instrumentation and test techniques.
NASA's B-52 carrier-launch vehicle was used to get the Pegasus airborne during six launches from 1990 to 1994. Thereafter, an Orbital Sciences L-1011 aircraft launched the Pegasus. The Pegasus launch vehicle itself has a 400- to 600-pound payload capacity in a 61-cubic-foot payload space at the front of the vehicle. The vehicle is capable of placing a payload into low earth orbit. This vehicle is 49 feet long and 50 inches in diameter. It has a wing span of 22 feet. (There is also a Pegasus XL vehicle that was introduced in 1994. Dryden has never launched one of these vehicles, but they have greater thrust and are 56 feet long.)
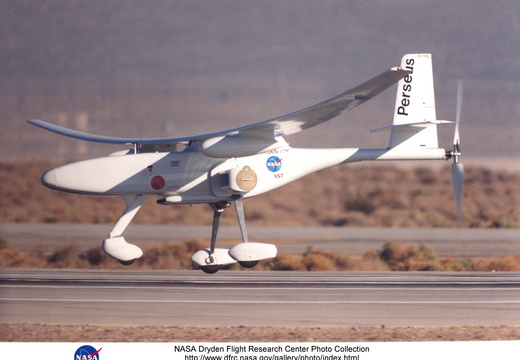
Perseus
The objectives of Perseus B's ERAST flight tests have been to reach and maintain horizontal flight above altitudes of 60,000 feet and demonstrate the capability to fly missions lasting from 8 to 24 hours, depending on payload and altitude requirements. The Perseus B aircraft established an unofficial altitude record for a single-engine, propeller-driven, remotely piloted aircraft on June 27, 1998. It reached an altitude of 60,280 feet. In 1999, several modifications were made to the Perseus aircraft including engine, avionics, and flight-control-system improvements. These improvements were evaluated in a series of operational readiness and test missions at the Dryden Flight Research Center, Edwards, California.
Perseus is a high-wing monoplane with a conventional tail design. Its narrow, straight, high-aspect-ratio wing is mounted atop the fuselage. The aircraft is pusher-designed with the propeller mounted in the rear. This design allows for interchangeable scientific-instrument payloads to be placed in the forward fuselage. The design also allows for unobstructed airflow to the sensors and other devices mounted in the payload compartment.
The Perseus B that underwent test and development in 1999 was the third generation of the Perseus design, which began with the Perseus Proof-Of-Concept aircraft. Perseus was initially developed as part of NASA's Small High-Altitude Science Aircraft (SHASA) program, which later evolved into the ERAST project. The Perseus Proof-Of-Concept aircraft first flew in November 1991 and made three low-altitude flights within a month to validate the Perseus aerodynamic model and flight control systems.
Next came the redesigned Perseus A, which incorporated a closed-cycle combustion system that mixed oxygen carried aboard the aircraft with engine exhaust to compensate for the thin air at high altitudes. The Perseus A was towed into the air by a ground vehicle and its engine started after it became airborne. Prior to landing, the engine was stopped, the propeller locked in horizontal position, and the Perseus A glided to a landing on its unique bicycle-type landing gear. Two Perseus A aircraft were built and made 21 flights in 1993-1994. One of the Perseus A aircraft reached over 50,000 feet in altitude on its third test flight. Although one of the Perseus A aircraft was destroyed in a crash after a vertical gyroscope failed in flight, the other aircraft completed its test program and remains on display at Aurora's facility in Manassas.
Perseus B first flew Oct. 7, 1994, and made two flights in 1996 before being damaged in a hard landing on the dry lakebed after a propeller shaft failure. After a number of improvements and upgrades—including extending the original 58.5-foot wingspan to 71.5 feet to enhance high-altitude performance--the Perseus B returned to Dryden in the spring of 1998 for a series of four flights. Thereafter, a series of modifications were made including external fuel pods on the wing that more than doubled the fuel capacity to 100 gallons. Engine power was increased by more than 20 percent by boosting the turbocharger output. Fuel consumption was reduced with fuel control modifications and a leaner fuel-air mixture that did not compromise power. The aircraft again crashed on Oct. 1, 1999, near Barstow, California, suffering moderate damage to the aircraft but no property damage, fire, or injuries in the area of the crash.
Perseus B is flown remotely by a pilot from a mobile flight control station on the ground. A Global Positioning System (GPS) unit provides navigation data for continuous and precise location during flight. The ground control station features dual independent consoles for aircraft control and systems monitoring. A flight termination system, required for all remotely piloted aircraft being flown in military-restricted airspace, includes a parachute system deployed on command plus a C-Band radar beacon and a Mode-C transponder to aid in location.
Dryden has provided hanger and office space for the Perseus B aircraft and for the flight test development team when on site for flight or ground testing. NASA's ERAST project is developing aeronautical technologies for a new generation of remotely piloted and autonomous aircraft for a variety of upper-atmospheric science missions and commercial applications. Dryden is the lead center in NASA for ERAST management and operations.
Perseus B is approximately 25 feet long, has a wingspan of 71.5 feet, and stands 12 feet high. Perseus B is powered by a Rotax 914, four-cylinder piston engine mounted in the mid-fuselage area and integrated with an Aurora-designed three-stage turbocharger, connected to a lightweight two-blade propeller.
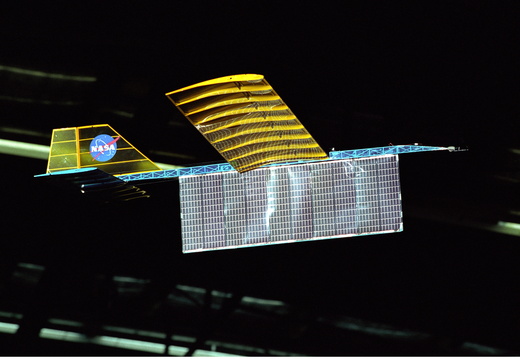
Power Beaming
Researchers from NASA's Marshall Space Flight Center, Huntsville, Alabama, and Dryden Flight Research Center, Edwards, California, and the University of Alabama in Huntsville have flight-demonstrated a small-scale aircraft that flies solely by means of propulsive power from an invisible, ground-based infrared laser.
Flights of the lightweight, radio-controlled model airplane inside a large building at NASA Marshall are believed to be the first time that a plane has been powered only by laser energy. The demonstration was a key step toward the capability to beam power to an aircraft, allowing it to stay in flight indefinitely -- a concept with potential for the scientific community as well as the remote sensing and telecommunications industries.
During the flight demonstration in September 2003, an engineer manually directed the laser's energy beam from a central platform at infrared-sensitive photovoltaic cells carried on a panel on the bottom of the aircraft to power the motor as it flew circles inside the large building.
A similar demonstration using a large theatrical spotlight was flown in the summer of 2002 at NASA Dryden, proving that beamed visible light could be used to power the 11-ounce aircraft. The spotlight beamed power to a solar panel attached underneath the aircraft frame that converted the light into electrical energy for the tiny, six-watt motor.
An aircraft was flown using microwave energy 20 years ago, but these were the first known demonstrations of beamed light energy to fly an airplane. The lightweight model aircraft used for these demonstrations was controlled using the same over-the-counter radio control instrumentation available to model aircraft hobby enthusiasts.
Beaming power via a laser to an aircraft is just one concept being explored by NASA to enable solar-electric powered aircraft to fly through the night when solar energy is not available. Another promising technology that is well along in development would use either regenerative or non-regenerative fuel cell systems to achieve the same purpose.
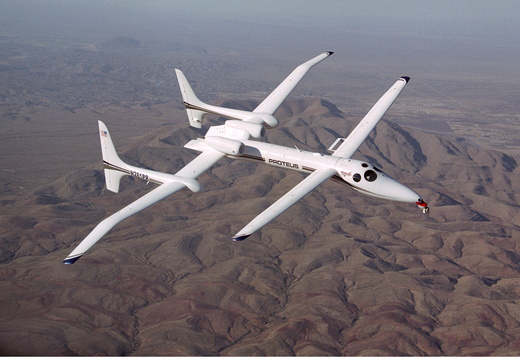
Proteus
The Proteus is a unique aircraft, designed as a high-altitude, long-duration telecommunications relay platform with potential for use on atmospheric sampling and Earth-monitoring science missions. Designed by Burt Rutan, president of Scaled Composites, LLC, of Mojave, Calif., Proteus is an "optionally piloted" aircraft ordinarily flown by two pilots in a pressurized cabin. However, it also has the capability to perform its missions semi-autonomously or flown remotely from the ground.
The aircraft is designed to cruise at altitudes from 59,000 to more than 65,000 feet for up to 18 hours. It was designed to carry an 18-foot diameter telecommunications antenna system for relay of broadband data over major cities. The design allows Proteus to be reconfigured for a variety of other missions such as atmospheric research, reconnaissance, commercial imaging, and launch of small space satellites. It is designed for extreme reliability and low operating costs, and to operate out of general aviation airports with minimal support.
Proteus has an all-composite airframe with graphite-epoxy sandwich construction. Its wingspan of 77 feet 7 inches is expandable to 92 feet with removable wingtips installed. Proteus is 56.3 feet long, 17.6 feet high and weighs 5,900 pounds empty. Proteus is powered by two Williams FJ44-2 turbofan engines, each rated at 2,300 pounds of thrust.
Flight testing of the Proteus began in the summer of 1998 at Mojave Airport and continued through the end of 1999.
Under NASA's Environmental Research Aircraft and Sensor Technology (ERAST) project, NASA's Dryden Flight Research Center assisted Scaled Composites in developing a sophisticated station-keeping autopilot system and a satellite communications (SATCOM)-based uplink-downlink data system for Proteus' performance and payload data.
Flight testing included the installation and checkout of the autopilot system, including the refinement of the altitude hold and altitude change software. The SATCOM equipment, including avionics and antenna systems, was installed and checked out in several flight tests. The systems performed flawlessly during Proteus' deployment to the Paris Airshow in 1999.
NASA has used Proteus as a testbed for a variety of technologies related to maturing unmanned air vehicles (UAVs) for use in civil applications.
A small Airborne Real-Time Imaging System (ARTIS) camera, developed by HyperSpectral Sciences, Inc., under NASA's ERAST project, was demonstrated during the summer of 1999 when it took visual and near-infrared photos from Proteus while it was flying high over the Experimental Aircraft Association's "AirVenture 99" Airshow at Oshkosh, Wisc. The images were displayed on a computer monitor at the show only moments after they were taken.
In March 2002, NASA Dryden, in cooperation with New Mexico State University's Technical Analysis and Applications Center (TAAC), the FAA and several other entities, conducted flight demonstrations of an active detect, see and avoid (DSA) system for potential application to unmanned aerial vehicles (UAVs) out of Las Cruces, New Mexico. Proteus was flown as a surrogate UAV controlled remotely from the ground, although safety pilots were aboard to handle takeoff and landing and any potential emergencies. Three other aircraft, ranging from general aviation aircraft to a NASA F/A-18, served as "cooperative" target aircraft with an operating transponder.
In each of 18 different scenarios, a Goodrich Skywatch HP Traffic Advisory System (TAS) on the Proteus detected approaching air traffic on potential collision courses, including several scenarios with two aircraft approaching from different directions. The remote pilot then directed Proteus to turn, climb or descend as needed to avoid the potential threat.
In April 2003, a second series of flight demonstrations focusing on "non-cooperative" aircraft (those without operating transponders), was conducted in restricted airspace near Mojave, Calif., again using the Proteus as a surrogate UAV. Proteus was equipped with a small Amphitech OASys 35 Ghz primary radar system to detect potential intruder aircraft on simulated collision courses. The radar data was telemetered directly to the ground station as well as via an Inmarsat satellite system installed on Proteus. A mix of seven intruder aircraft, ranging from a sailplane to a high-speed jet, flew 20 scenarios over a four-day period, one or two aircraft at a time. In each case, the radar picked up the intruding aircraft at ranges from 2.5 to 6.5 miles, depending on the intruder's radar signature. Proteus' remote pilot on the ground was able to direct Proteus to take evasive action if needed.
Based on the preliminary results of both series of tests, project engineers believe that some upgrades would have to be made to both the Skywatch and the OASys detection systems to maximize their effectiveness as collision-avoidance detection sensors for UAVs. Additional flight tests of other types of detection systems, such as electro-optical infrared devices, may occur in the future under a follow-on program in an effort to establish an equivalent level of safety for UAVs to that now required of manned aircraft.
The ERAST Project is sponsored by the Office of Aerospace Technology at NASA Headquarters, and is managed by the Dryden Flight Research Center, Edwards, Calif.
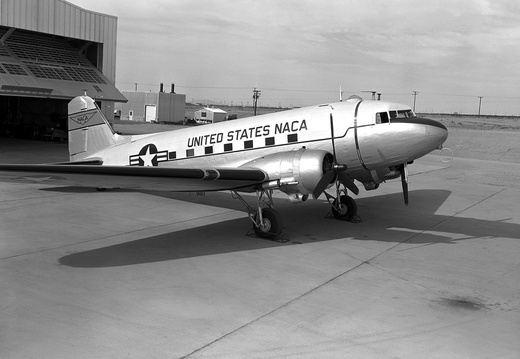
R4D Skytrain
Over the 32 years it was used at Edwards, three different R4D/C-47s were used to shuttle personnel and equipment between NACA/NASA Centers and test locations throughout the country and for other purposes. One purpose was landing on "dry" lakebeds to determine if their surfaces were hard (dry) enough for X-15 emergency landings.
The R4D/C-47 served a variety of needs, including serving as the first air-tow vehicle for the M2-F1 lifting body (which was built of mahogany plywood). The C-47 (as it was then called) was used for 77 tows before the M2-F1 was retired for more advanced lifting bodies that were dropped from the NASA B-52 "Mothership."
The R4D also served as a research aircraft. It was used to conduct early research on wing-tip-vortex flow visualization as well as checking out the NASA Uplink Control System. The first Gooney Bird was at the NACA High-Speed Flight Research Station (now the Dryden Flight Research Center) from 1952 to 1956 and flew at least one cross-country flight to the Langley Research Center, Hampton, Virginia. The second R4D, used from 1956 to 1979, made many flights to the Ames Research Center, Mountain View, California, and other NASA locations. The third R4D aircraft proved to be less reliable, causing continual maintenance problems. After an unplanned desert landing during a military exercise, it was sent to the Lewis Research Center, Cleveland, Ohio, (now the Glenn Research Center).
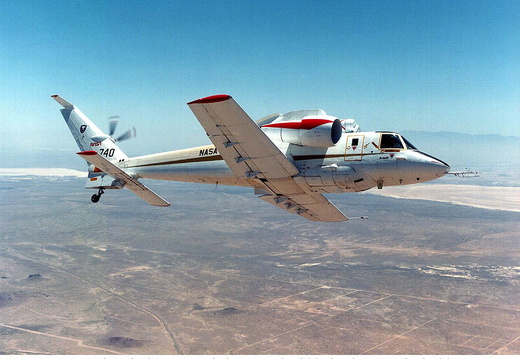
RSRA
A Rotor Systems Research Aircraft (RSRA) underwent limited ground and flight tests at the Dryden Flight Research Center, Edwards, California, in spring of 1984. The purpose of the tests were to train pilots and to verify and develop the design flight envelope established by the Sikorsky Aircraft Company.
The test aircraft had a basic helicopter fuselage with the wings and lower horizontal all-flying stabilizer installed. Two auxiliary power plants were mounted on either side of the fuselage. These GE TF-34's were used to offset drag effects when rotor systems were being tested with the aircraft in compound configuration, and to provide thrust for the airplane configuration.
The tests at Dryden were to familiarize pilots and researchers with the ground-handling and takeoff flight characteristics, as well as to acquire in-flight data in the aircraft configuration, with the main rotor removed. Tests were successful and lead to later rotor research conducted at NASA's Ames Research Center. One of the two RSRA aircraft was later modified to the X-Wing and received limited testing at Dryden before the program was terminated in 1988.
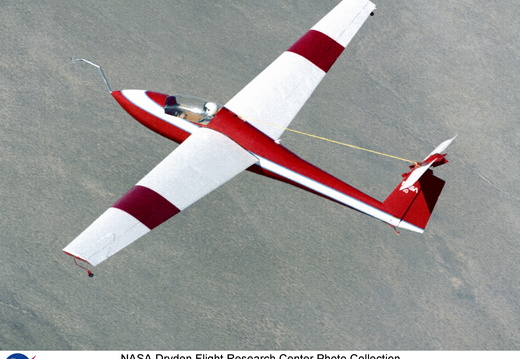
Schweizer 1-36
Schweizer modified the horizontal stabilizer (T-tail configuration) so that it could pivot as much as 70 degrees with the leading edge down. Once the aircraft arrived at ADFRF, it was further modified, including modification of the cockpit area to permit easier pilot egress and addition of a NASA instrumentation system in the fuselage. After the modifications were completed, radio-controlled-model and ground tests of the aircraft were performed prior to flight tests. These preliminary tests included use of a simulator.
In September and October 1983, the modified Schweizer SGS 1-36 was flown in the ADFRF’s high-angle-of-attack program. The Schweizer was chosen for the program because of its slow speed and because its high-angle-of-attack aerodynamics were dominated by long wings rather than a long, pointed nose or forward strake. The objectives of the program were to demonstrate the feasibility of piloted, controlled flight at very high angles of attack and to refine piloting techniques required to make a safe transition into, maneuver in, and recover from controlled flight at very high angles of attack. Of particular interest during the 20 flights of the sailplane were the stability-and-control derivatives, trim data, and piloting techniques required to safely enter and exit the very high-angle-of-attack flight regime.
For the flight test, the sailplane was typically towed to an altitude of 8,500 feet above ground level and released. Upon release the sailplane was decelerated to near-stall speed. The pilot then performed maneuvers to investigate handling qualities.
Flight data showed that piloting techniques for the sailplane allowed the pilot to safely make entry into, maneuver in, and recover from controlled flight within the 30- to 72-degree angle-of-attack range. Maximum likelihood analysis (parameter estimation) techniques were used to obtain aerodynamic derivatives from the flight test data. These data were compared to a predicted data set derived from wind tunnels. Generally, the agreement was fair to good, but the derivatives were used to refine the aerodynamic database at low and very high angles of attack. Analysis of the flight data was also used to better define the vehicle’s trim and operational performance envelope.
The Schweizer 1-36 sailplane is a single-place, mostly aluminum aircraft. The wingspan is close to 46 feet and the fuselage is nearly 21 feet long. The horizontal stabilizer is a T-tail configuration with a span of 7.9 feet.
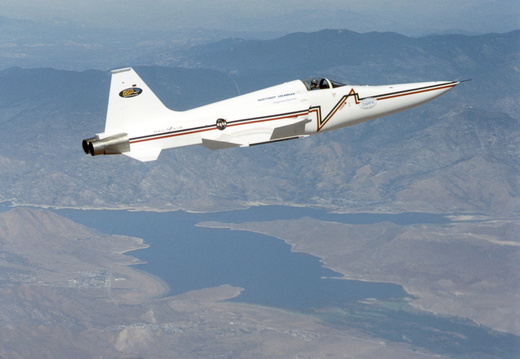
Shaped Sonic Boom Demonstration
The project is an effort to lessen sonic booms.
During the recent demonstration, the F-15B flew behind the modified F-5E sonic boom demonstrator aircraft in order to measure the aircraft's sonic boom characteristics.
Flying behind and below the F-5E, and using its specially-instrumented nose boom, the F-15B recorded many shockwave patterns from the F-5E at various distances and orientations from the aircraft.
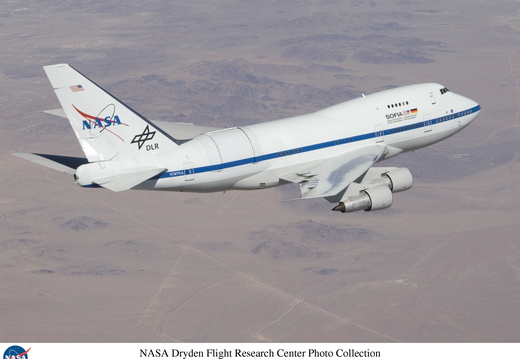
SOFIA
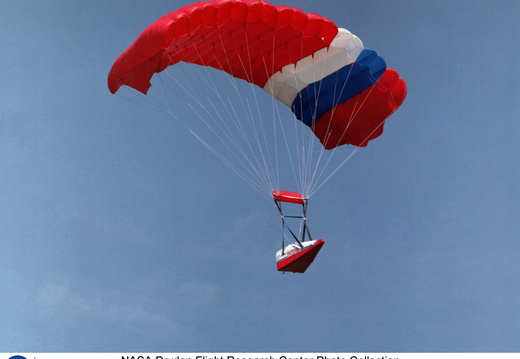
Spacewedge
The Johnson Space Center and the U.S. Army participated in various phases of the program. The Charles Stark Draper Laboratory developed the software for Wedge 3 under contract to the Army. Four generic spacecraft (each called a Spacewedge or simply a Wedge) were built; the last one was built to test the feasibility of a parafoil for delivering Army cargoes.
Technology developed during this program has applications for future spacecraft recovery systems, such as the X-38 Crew Return Vehicle demonstrator. The Spacewedge program demonstrated precision flare and landing into the wind at a predetermined location. The program showed that a flexible, deployable system using autonomous navigation and landing was a viable and practical way to recover spacecraft.
NASA researchers conducted flight tests of the Spacewedge at three sites near Dryden, a hillside near Tehachapi, the Rogers Dry Lakebed at Edwards Air Force Base, and the California City Airport Drop Zone. During the first phase of testing 36 flights were made. Phase II consisted of 45 flights using a smaller parafoil. A third Phase of 34 flights was conducted primarily by the Army and resulted in the development of an Army guidance system for precision offset cargo delivery. The wedge used during the Army phase was not called a Spacewedge but simply a Wedge.
The Spacewedge was a flattened biconical airframe joined to a ram-air parafoil with a custom harness. In the manual control mode, the vehicle was flown using a radio uplink. In its autonomous mode, it was controlled using a small computer that received input from onboard sensors. Selected sensor data was recorded onto several onboard data loggers. Two Spacewedge shapes were used for four airframes representing generic hypersonic vehicle configurations. Spacewedge vehicles were 48 inches long, 30 inches wide, and 21 inches high. Their basic weight was 120 pounds, although different configurations weighed from 127 to 184 pounds.
Potential uses for Spacewedge-based technology include deployable, precision, autonomous landing systems, such as the one deployed by the X-38 crew return vehicle; planetary probes; booster recovery systems; autonomous gliding parachute systems on military aircraft ejection seats; offset delivery of military cargoes; and delivery of humanitarian aid to hard-to-reach locations.
Dryden employees involved with the Spacewedge program included R. Dale Reed, who originated the concept of conducting a subscale flight test at Dryden and participated in the actual testing. Alexander Sim managed the flight project and participated in its documentation. James Murray served as the principal Dryden investigator and as the lead for all systems integration for Phases I and II (the Spacewedge phases).
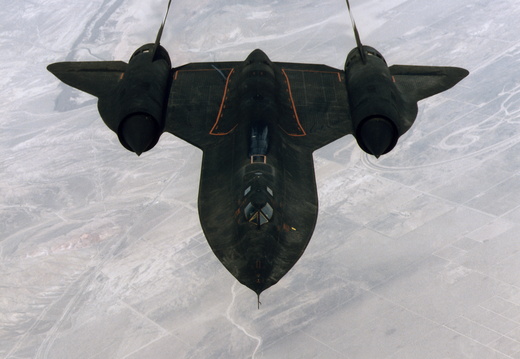
SR-71
As research platforms, the aircraft can cruise at Mach 3 for more than one hour. For thermal experiments, this can produce heat soak temperatures of over 600 degrees Fahrenheit (F). This operating environment makes these aircraft excellent platforms to carry out research and experiments in a variety of areas -- aerodynamics, propulsion, structures, thermal protection materials, high-speed and high-temperature instrumentation, atmospheric studies, and sonic boom characterization.
The SR-71 was used in a program to study ways of reducing sonic booms or over pressures that are heard on the ground, much like sharp thunderclaps, when an aircraft exceeds the speed of sound. Data from this Sonic Boom Mitigation Study could eventually lead to aircraft designs that would reduce the "peak" overpressures of sonic booms and minimize the startling affect they produce on the ground.
One of the first major experiments to be flown in the NASA SR-71 program was a laser air data collection system. It used laser light instead of air pressure to produce airspeed and attitude reference data, such as angle of attack and sideslip, which are normally obtained with small tubes and vanes extending into the airstream.
One of Dryden's SR-71s was used for the Linear Aerospike Rocket Engine, or LASRE Experiment. Another earlier project consisted of a series of flights using the SR-71 as a science camera platform for NASA's Jet Propulsion Laboratory in Pasadena, California. An upward-looking ultraviolet video camera placed in the SR-71’s nosebay studied a variety of celestial objects in wavelengths that are blocked to ground-based astronomers.
Earlier in its history, Dryden had a decade of past experience at sustained speeds above Mach 3. Two YF-12A aircraft and an SR-71 designated as a YF-12C were flown at the center between December 1969 and November 1979 in a joint NASA/USAF program to learn more about the capabilities and limitations of high-speed, high-altitude flight. The YF-12As were prototypes of a planned interceptor aircraft based on a design that later evolved into the SR-71 reconnaissance aircraft. Dave Lux was the NASA SR-71 project manger for much of the decade of the 1990s, followed by Steve Schmidt.
Developed for the USAF as reconnaissance aircraft more than 30 years ago, SR-71s are still the world's fastest and highest-flying production aircraft. The aircraft can fly at speeds of more than 2,200 miles per hour (Mach 3+, or more than three times the speed of sound) and at altitudes of over 85,000 feet.
The Lockheed Skunk Works (now Lockheed Martin) built the original SR-71 aircraft. Each aircraft is 107.4 feet long, has a wingspan of 55.6 feet, and is 18.5 feet high (from the ground to the top of the rudders, when parked). Gross takeoff weight is about 140,000 pounds, including a possible fuel weight of 80,280 pounds. The airframes are built almost entirely of titanium and titanium alloys to withstand heat generated by sustained Mach 3 flight. Aerodynamic control surfaces consist of all-moving vertical tail surfaces, ailerons on the outer wings, and elevators on the trailing edges between the engine exhaust nozzles.
The two SR-71s at Dryden have been assigned the following NASA tail numbers: NASA 844 (A model), military serial 61-7980 and NASA 831 (B model), military serial 61-7956. From 1990 through 1994, Dryden also had another "A" model, NASA 832, military serial 61-7971. This aircraft was returned to the USAF inventory and was the first aircraft reactivated for USAF reconnaissance purposes in 1995. It has since returned to Dryden along with SR-71A 61-7967.
The last SR-71 flight was made on Saturday October 9, 1999, at the Edwards AFB air show. The aircraft used was NASA 844. The aircraft was also scheduled to make a flight the following day, but a fuel leak grounded the aircraft and prevented it from flying again. The NASA SR-71s were then put in flyable storage, where they remained until 2002. They were then sent to museums.
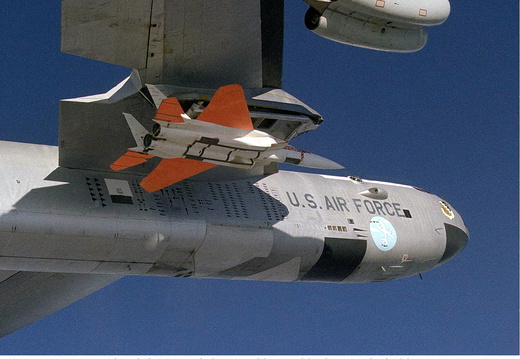
SRV
Altitudes ranging from 16,000 to 1000 meters were flown with the unpowered SRV with angles of attack ranging from 88 degrees to -70 degrees in erect and inverted spins. Over 1200 turns were obtained in spins during the program, including one spin of 2.5 minues and 72 turns covering 12,000 meters of altitude. The high number of turns per spin allowed steady-state spin information to be obtained without creating risk or discomfort for a pilot.
The SRV was about 7 meters long and had a wingspan of about 4 meters. The aircraft was evaluated with many different control laws, most of which were developed flying qualities studies. The vehicle evaluated various forebody configurations and spin recovery devices.
The SRV was flown 27 times with each flight lasting about 10 minutes and concluding with a landing on the surface of Rogers Dry Lake. The SRV pilot flew the aircraft from a ground cockpit in the Remotely Piloted Research Vehicle Laboratory (RPRV) at Dryden. Landing was accomplished through the use of an onboard television camera.
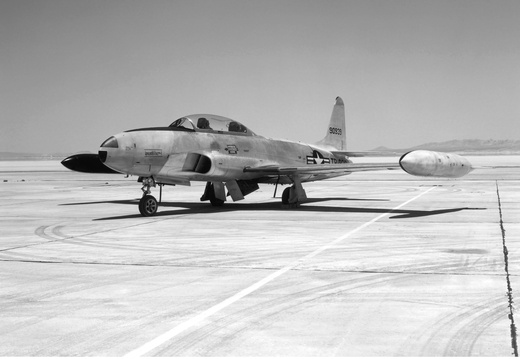
T-33
Four Lockheed T-33A jet trainers were operated from 1958 to 1973. They were used for support and flight research.
T-33A (49-0939) arrived at NACA High Speed Flight Station on February 5, 1958. It departed September 20, 1961 to Davis-Monthan AFB, Arizona for storage.
T-33A (51-4299) arrived at NASA Flight Research Center on April 25, 1961. It departed May 31, 1961 to Davis-Monthan AFB, Arizona for storage.
T-33A (51-6692) arrived at NASA Flight Research Center on June 2, 1961. It was destroyed in a non-fatal crash December 26, 1962.
T-33A (55-4351) (NASA 815) arrived at NASA Flight Research Center on January 9, 1963. It was used in a monocular vision study. It departed September 10, 1973 to Redding, California.
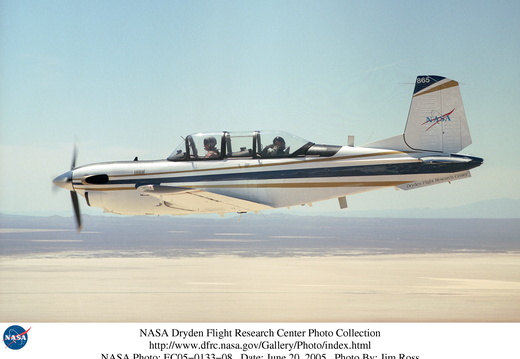
T-34C
Mission support aircraft such as the T-34C accompany research flights for photography and video data collection, and also as safety chase. At Dryden, the T-34C is primarily used for chasing remotely piloted unmanned air vehicles which fly slower than NASA's F-18's mission support aircraft can fly. It is also used for required pilot proficiency flying.
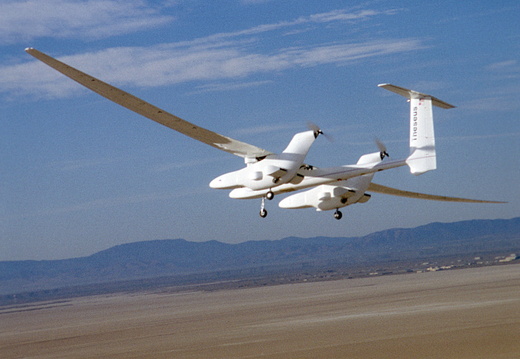
Theseus
The Theseus remotely piloted aircraft flew its maiden flight on May 24, 1996, at Dryden. During its sixth flight on November 12, 1996, Theseus experienced an in-flight structural failure that resulted in the loss of the aircraft. As of the beginning of the year 2000, Aurora had not rebuilt the aircraft.
Theseus was built for NASA under an innovative, $4.9 million fixed-price contract by Aurora Flight Sciences Corporation and its partners, West Virginia University, Morgantown, West Virginia, and Fairmont State College, Fairmont, West Virginia.
The twin-engine, unpiloted vehicle had a 140-foot wingspan, and was constructed largely of composite materials. Powered by two 80-horsepower, turbocharged piston engines that drove twin 9-foot-diameter propellers, Theseus was designed to fly autonomously at high altitudes, with takeoff and landing under the active control of a ground-based pilot in a ground control station "cockpit."
With the potential ability to carry 700 pounds of science instruments to altitudes above 60,000 feet for durations of greater than 24 hours, Theseus was intended to support research in areas such as stratospheric ozone depletion and the atmospheric effects of future high-speed civil transport aircraft engines. Instruments carried aboard Theseus also would be able to validate satellite-based global environmental change measurements. Dryden’s Project Manager was John Del Frate.
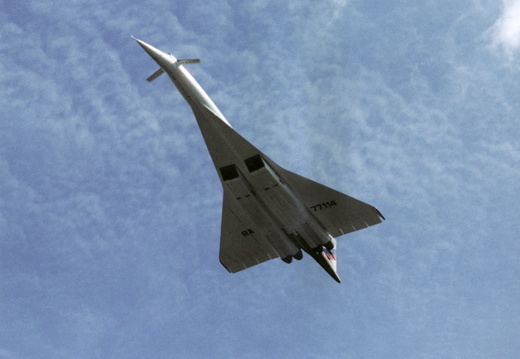
TU-144LL
The aircraft’s initial flight phase began in June 1996 and concluded in February 1998 after 19 research flights. A shorter follow-on program involving seven flights began in September 1998 and concluded in April 1999. All flights were conducted in Russia from Tupolev's facility at the Zhukovsky Air Development Center near Moscow.
The centerpiece of the research program was the Tu 144LL, a first-generation Russian supersonic jetliner that was modified by its developer/builder, Tupolev ANTK (aviatsionnyy nauchno-tekhnicheskiy kompleks–roughly, aviation technical complex), into a flying laboratory for supersonic research. Using the Tu-144LL to conduct flight research experiments, researchers compared full-scale supersonic aircraft flight data with results from models in wind tunnels, computer-aided techniques, and other flight tests. The experiments provided unique aerodynamic, structures, acoustics, and operating environment data on supersonic passenger aircraft.
Data collected from the research program was being used to develop the technology base for a proposed future American-built supersonic jetliner. Although actual development of such an advanced supersonic transport (SST) is currently on hold, commercial aviation experts estimate that a market for up to 500 such aircraft could develop by the third decade of the 21st Century.
The Tu-144LL used in the NASA-sponsored research program was a "D" model with different engines than were used in production-model aircraft. Fifty experiments were proposed for the program and eight were selected, including six flight and two ground (engine) tests. The flight experiments included studies of the aircraft’s exterior surface, internal structure, engine temperatures, boundary-layer airflow, the wing’s ground-effect characteristics, interior and exterior noise, handling qualities in various flight profiles, and in-flight structural flexibility. The ground tests studied the effect of air inlet structures on airflow entering the engine and the effect on engine performance when supersonic shock waves rapidly change position in the engine air inlet.
A second phase of testing further studied the original six in-flight experiments with additional instrumentation installed to assist in data acquisition and analysis. A new experiment aimed at measuring the in-flight deflections of the wing and fuselage was also conducted. American-supplied transducers and sensors were installed to measure nose boom pressures, angle of attack, and sideslip angles with increased accuracy. Two NASA pilots, Robert Rivers of Langley Research Center, Hampton, Virginia, and Gordon Fullerton from Dryden Flight Research Center, Edwards, California, assessed the aircraft’s handling at subsonic and supersonic speeds during three flight tests in September 1998. The program concluded after four more data-collection flights in the spring of 1999.
The Tu-144LL model had new Kuznetsov NK-321 turbofan engines rated at more than 55,000 pounds of thrust in full afterburner. The aircraft is 215 feet, 6 inches long and 42 feet, 2 inches high with a wingspan of 94 feet, 6 inches. The aircraft is constructed mostly of light aluminum alloy with titanium and stainless steel on the leading edges, elevons, rudder, and the under-surface of the rear fuselage.
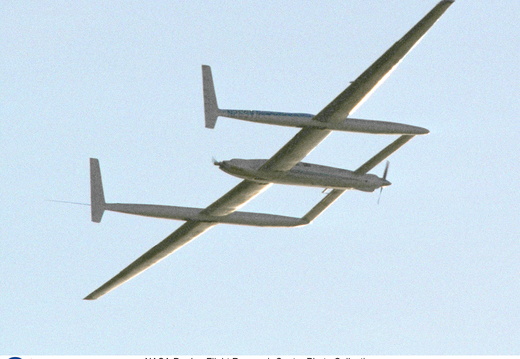
Voyager
Richard Rutan and Jeana Yeager piloted the aircraft from a cramped cockpit. Voyager's takeoff weight was more than 10 times the structural weight, but its drag was lower than almost any other powered aircraft.
The aircraft's design and light-weight structural materials allowed it to carry an unprecedented amount of fuel on its 25,000 mile flight. Voyager took off from Edwards Dec. 14, and traveled at an average speed of 115.8 mph. The 9 day, 3 minute, 44 sec. flight nearly doubled the previous distance record set in 1962 by a USAF/Boeing B-52H.
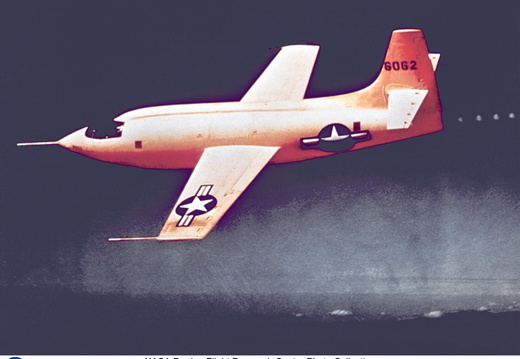
X-1
The X-1 Program was originally designated the XS-1 for EXperimental Sonic. The X-1’s mission was to investigate the transonic speed range (speeds from just below to just above the speed of sound) and, if possible, to break the "sound barrier." Three different X-1s were built and designated: X-1-1, X-1-2 (later modified to become the X-1E), and X-1-3. The basic X-1 aircraft were flown by a large number of different pilots from 1946 to 1951.
The X-1 Program not only proved that humans could go beyond the speed of sound, it reinforced the understanding that technological barriers could be overcome. The X-1s pioneered many structural and aerodynamic advances including extremely thin, yet extremely strong wing sections; supersonic fuselage configurations; control system requirements; powerplant compatibility; and cockpit environments. The X-1 aircraft were the first transonic-capable aircraft to use an all-moving stabilizer. The flights of the X-1s opened up a new era in aviation.
The first X-1 was air-launched unpowered from a Boeing B-29 Superfortress on Jan. 25, 1946. Powered flights began in December 1946. On Oct. 14, 1947, the X-1-1, piloted by Air Force Captain Charles "Chuck" Yeager, became the first aircraft to exceed the speed of sound, reaching about 700 miles per hour (Mach 1.06) and an altitude of 43,000 feet.
The number 2 X-1 was modified and redesignated the X-1E. The modifications included adding a conventional canopy, an ejection seat, a low-pressure fuel system of increased capacity, and a thinner high-speed wing.
The X-1E was used to obtain in-flight data at twice the speed of sound, with particular emphasis placed on investigating the improvements achieved with the high-speed wing. These wings, made by Stanley Aircraft, were only 3 3/8-inches thick at the root and had 343 gauges installed in them to measure structural loads and aerodynamic heating.
The X-1E used its rocket engine to power it up to a speed of 1,471 miles per hour (Mach 2.24) and to an altitude of 73,000 feet. Like the X-1 it was air-launched.
The X-1 aircraft were almost 31 feet long and had a wingspan of 28 feet. The X-1 was built of conventional aluminum stressed-skin construction to extremely high structural standards. The X-1E was also 31 feet long but had a wingspan of only 22 feet, 10 inches. It was powered by a Reaction Motors, Inc., XLR-8-RM-5, four-chamber rocket engine. As did all X-1 rocket engines, the LR-8-RM-5 engine did not have throttle capability, but instead, depended on ignition of any one chamber or group of chambers to vary speed.
There were also X-1A, X-1B, and and a short-lived X-1D models of the X-1.
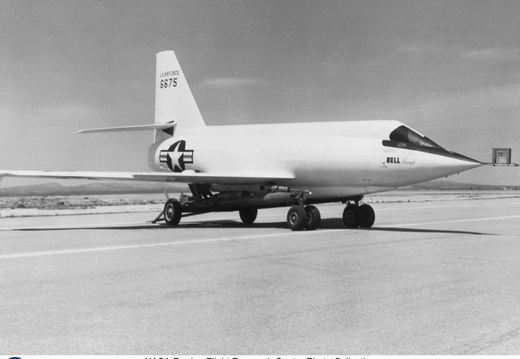
X-2
The X-2 #1 (46-674) made its first unpowered glide flight on Aug. 5 1954. This aircraft made a total of seventeen flights before
it was lost on Sept. 27 1956. Its pilot, Capt. Milburn Apt, USAF, had flown to a record speed of Mach 3.2 or 2,094 mph thereby becoming the first person to exceed Mach 3.
The X-2 #2 (46-675) was lost in an inflight explosion while at the Bell plant during captive flight trials and was jettisoned into Lake Ontario in 1953.
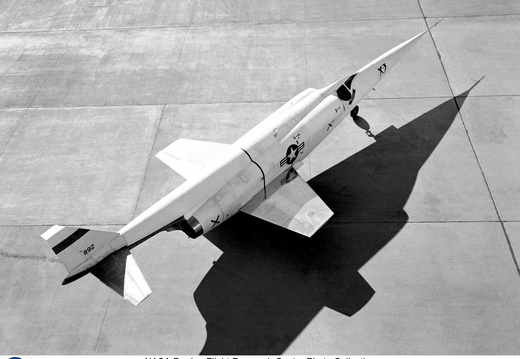
X-3
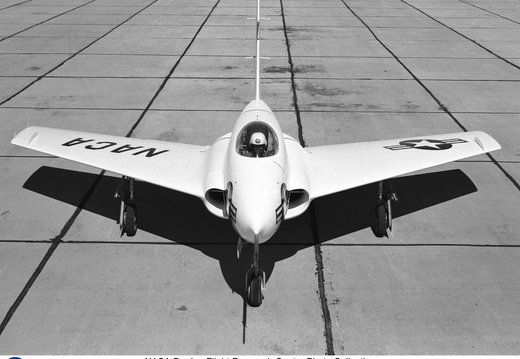
X-4
Northrop Aircraft, Inc. built two X-4 aircraft, the first of which proved to be mechanically unsound. However, ship number 2, with a thicker trailing edge on the wings and elevon, was very reliable. Ship 1 was then grounded and used as parts for ship 2. While being tested from 1950 to 1953 at the NACA High-Speed Flight Research Station (predecessor of today’s NASA Dryden Flight Research Center, Edwards, California), the X-4’s semi-tailless configuration exhibited inherent longitudinal stability problems (porpoising) as it approached the speed of sound.
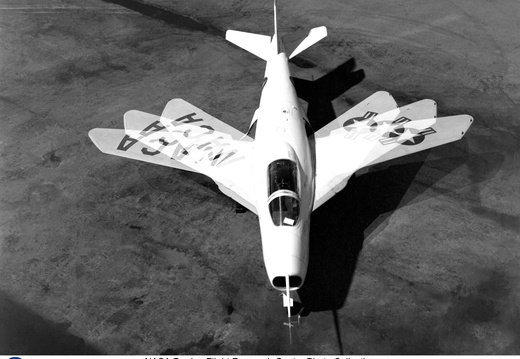
X-5
There were two X-5 vehicles. Ship 1 was flown at the NACA High-Speed Flight Research Station (High-Speed Flight Station, as it was redesignated in 1954) from 1951 to 1955. Ship 2 was operated by Bell and the U.S. Air Force and was lost in a spin accident in 1953.
Following the conclusion of the contractor’s test program, the X-5 was grounded for installation of a NACA instrument package. The Air Force conducted a short, six-flight, evaluation program. Since the Air Force evaluation program included data collection, it was considered as part of the overall NACA effort and flights were logged as AF/NACA. In the NACA test program, the X-5 demonstrated severe stall-spin instability. The X-5 was also used as a chase plane for other research aircraft because it could vary its flying characteristics to suit the airplane it was chasing. Ship 1 flew a total of 133 flights during its three years of service.
In spite of the problems with the aircraft, the X-5 provided a significant full-scale verification of NACA wind-tunnel predictions for reduced drag and improved performance that resulted from this configuration’s increasing the wing sweep as the speed of the aircraft approached the speed of sound. The X-5 flight tests provided some of the design data for the Air Force F-111 and Navy F-14 tactical aircraft. Although the mechanism by which the X-5 changed its wing sweep made this particular design impractical, development of a viable variable-sweep aircraft had to await Langley Aeronautical Laboratory’s concept of an outboard wing pivot in the mid-1950s. (Langley was a NACA research laboratory in Hampton, Virginia.)
The X-5 was a single seat aircraft powered by an Allison J-35-A-17A jet engine. It was 33.33 feet long with a wingspan of 20.9 feet (with the wings swept back at an angle of 60 degrees) to 33.5 feet (with the wings unswept). When fully fueled, the X-5 weighed 9,875 pounds.
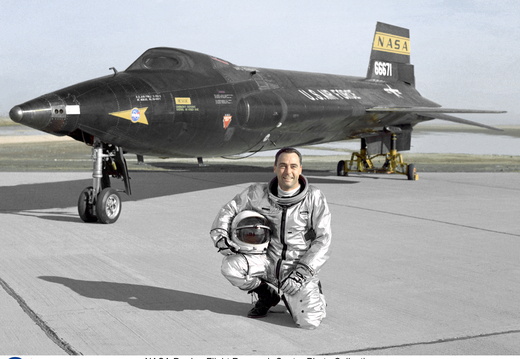
X-15
The X-15 research aircraft was developed to provide in-flight information and data on aerodynamics, structures, flight controls, and the physiological aspects of high-speed, high-altitude flight. A follow-on program used the aircraft as a testbed to carry various scientific experiments beyond the Earth's atmosphere on a repeated basis.
For flight in the dense air of the usable atmosphere, the X-15 used conventional aerodynamic controls such as rudder surfaces on the vertical stabilizers to control yaw and canted horizontal surfaces on the tail to control pitch when moving in synchronization or roll when moved differentially.
For flight in the thin air outside of the appreciable Earth's atmosphere, the X-15 used a reaction control system. Hydrogen peroxide thrust rockets located on the nose of the aircraft provided pitch and yaw control. Those on the wings provided roll control.
Because of the large fuel consumption, the X-15 was air launched from a B-52 aircraft at 45,000 ft and a speed of about 500 mph. Depending on the mission, the rocket engine provided thrust for the first 80 to 120 sec of flight. The remainder of the normal 10 to 11 min. flight was powerless and ended with a 200-mph glide landing.
Generally, one of two types of X-15 flight profiles was used: a high-altitude flight plan that called for the pilot to maintain a steep rate of climb, or a speed profile that called for the pilot to push over and maintain a level altitude.
The X-15 was flown over a period of nearly 10 years--June 1959 to Oct. 1968--and set the world's unofficial speed and altitude records of 4,520 mph (Mach 6.7) and 354,200 ft (over 67 mi) in a program to investigate all aspects of piloted hypersonic flight. Information gained from the highly successful X-15 program contributed to the development of the Mercury, Gemini, and Apollo manned spaceflight programs, and also the Space Shuttle program.
The X-15s made a total of 199 flights and were manufactured by North American Aviation.
X-15-1, serial number 56-6670, is now located at the National Air and Space Museum, Washington DC.
North American X-15A-2, serial number 56-6671, is at the United States Air Force Museum, Wright-Patterson AFB, Ohio. The X-15-3, serial number 56-6672, crashed on 15 November 1967, resulting in the death of Maj. Michael J. Adams.
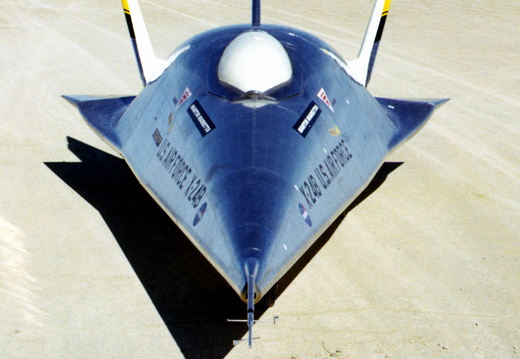
X-24
Lifting bodies’ aerodynamic lift, essential to flight in the atmosphere, was obtained from their shape. The addition of fins and control surfaces allowed the pilots to stabilize and control the vehicles and regulate their flight paths.
Built by Martin Aircraft Company, Maryland, for the U.S. Air Force, the X-24A was a bulbous vehicle shaped like a teardrop with three vertical fins at the rear for directional control. It weighed 6,270 pounds, was 24.5 feet long and 11.5 feet wide (measuring just the fuselage, not the distance between the tips of the outboard fins). Its first unpowered glide flight was on April 17, 1969, with Air Force Maj. Jerauld Gentry at the controls. Gentry also piloted its first powered flight on March 19, 1970.
The X-24A was flown 28 times in the program that, like the HL-10, validated the concept that a Space Shuttle vehicle could be landed unpowered. The fastest speed achieved by the X-24A was 1,036 miles per hour (mph--Mach 1.6). Its maximum altitude was 71,400 feet. It was powered by an XLR-11 rocket engine with a maximum theoretical vacuum thrust of 8,480 pounds.
The X-24A was later modified into the X-24B. The bulbous shape of the X-24A was converted into a "flying flatiron" shape with a rounded top, flat bottom, and double delta platform that ended in a pointed nose. The X-24B demonstrated that accurate unpowered reentry vehicle landings were operationally feasible. Top speed achieved by the X-24B was 1,164 mph and the highest altitude it reached was 74,130 feet. The vehicle is on display at the Air Force Museum, Wright-Patterson Air Force Base, Ohio. The pilot on the last powered flight of the X-24B was Bill Dana, who also flew the last X-15 flight about seven years earlier.
The X-24A shape was later borrowed for the X-38 Crew Return Vehicle (CRV) technology demonstrator for the International Space Station.
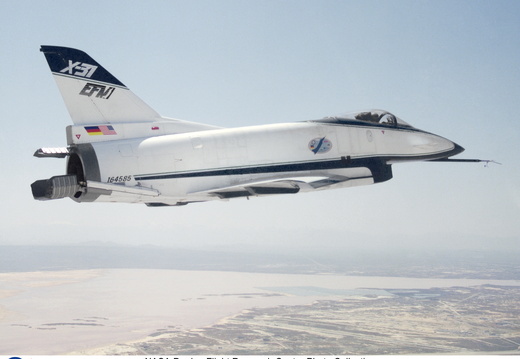
X-31
This program demonstrated the value of using thrust vectoring (directing engine exhaust flow) coupled with an advanced flight control system to provide controlled flight to very high angles of attack. The result was a significant advantage over most conventional fighters in close-in combat situations. The X-31 flight program focused on agile flight within the post-stall regime, producing technical data to give aircraft designers a better understanding of aerodynamics, effectiveness of flight controls and thrust vectoring, and airflow phenomena at high angles of attack.
Stall is a condition of an airplane or an airfoil in which lift decreases and drag increases due to the separation of airflow. Thrust vectoring compensates for the loss of control through normal aerodynamic surfaces that occurs during a stall. Post-stall refers to flying beyond the normal stall angle of attack, which in the X-31 was at a 30-degree angle of attack.
During Dryden flight testing, the X-31 aircraft established several milestones. On November 6, 1992, the X-31 achieved controlled flight at a 70-degree angle of attack. On April 29, 1993, the second X-31 successfully executed a rapid minimum-radius, 180-degree turn using a post-stall maneuver, flying well beyond the aerodynamic limits of any conventional aircraft. This revolutionary maneuver has been called the "Herbst Maneuver" after Wolfgang Herbst, a German proponent of using post-stall flight in air-to-air combat. It is also called a "J Turn" when flown to an arbitrary heading change.
The aircraft was flown in tactical maneuvers against an F/A-18 and other tactical aircraft as part of the test flight program. During November and December 1993, the X-31 reached a supersonic speed of Mach 1.28. In 1994, the X-31 program installed software to demonstrate quasi-tailless operation.
The X-31 flight test program was conducted by an international test organization (ITO) managed by the Advanced Research Projects Office (ARPA), known as the Defense Advanced Research Projects Office (DARPA) before March 1993. The ITO included the U.S. Navy and U.S. Air Force, Rockwell Aerospace, the Federal Republic of Germany, Daimler-Benz (formerly Messerschmitt-Bolkow-Blohm and Deutsche Aerospace), and NASA. Gary Trippensee was the ITO director and NASA Project Manager. Pilots came from participating organizations.
The X-31 was 43.33 feet long with a wingspan of 23.83 feet. It was powered by a single General Electric P404-GE-400 turbofan engine that produced 16,000 pounds of thrust in afterburner.
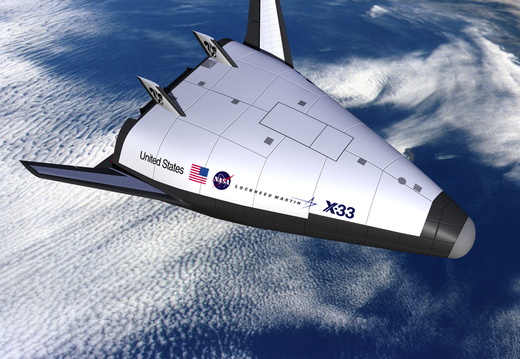
X-33
NASA Headquarter's Office of Space Access and Technology oversaw the RLV program, which was managed by the RLV Office at NASA's Marshall Space Flight Center, located in Huntsville, Alabama. Responsibilities of other NASA Centers include: Johnson Space Center, Houston, Texas, guidance navigation and control technology, manned space systems, and health technology; Ames Research Center, Mountain View, CA., thermal protection system testing; Langley Research Center, Langley, Virginia, wind tunnel testing and aerodynamic analysis; and Kennedy Space Center, Florida, RLV operations and health management.
Lockheed Martin's industry partners in the X-33 program were: Astronautics, Inc., Denver, Colorado, and Huntsville, Alabama; Engineering & Science Services, Houston, Texas; Manned Space Systems, New Orleans, LA; Sanders, Nashua, NH; and Space Operations, Titusville, Florida. Other industry partners are: Rocketdyne, Canoga Park, California; Allied Signal Aerospace, Teterboro, NJ; Rohr, Inc., Chula Vista, California; and Sverdrup Inc., St. Louis, Missouri.
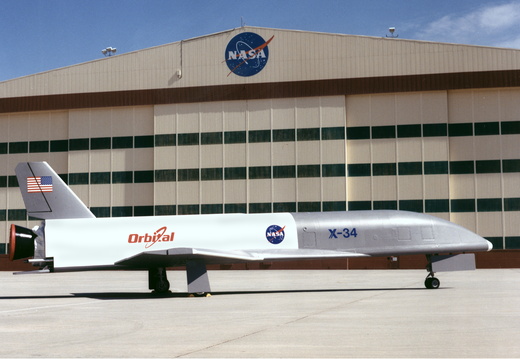
X-34
The unpiloted X-34 is a technology testbed demonstrator that is designed to demonstrate key vehicle and operational technologies applicable to future low-cost reusable launch vehicles. The vehicle structure is all-composite with a one-piece delta wing design. The vehicle is 58.3 feet long and has a 27.7-foot wingspan.
The suborbital vehicle was designed and built by Orbital Sciences Corporation, Dulles, Virginia, and is powered by an oxygen and kerosene Fastrac engine that was designed and built by NASA�s Marshall Space Flight Center (MSFC), Huntsville, Alabama. Fastrac is only the second American-made engine of the 29 engines developed in the last 25 years. The vehicle is designed to reach speeds of up to Mach 8 and altitudes of up to approximately 250,000 feet. Specific technologies built into the vehicle include composite structures, composite reusable propellant fuel tanks, an advanced thermal protection system, low-cost avionics, leading-edge tiles, and autonomous flight operation systems.
The project�s goal is to reduce the cost of launching payloads into orbit from $10,000 per pound today to one of $1,000 per pound, thereby improving U.S. economic competitiveness. NASA and Orbital, using a small workforce, plan to demonstrate the ability to fly the X-34 every two weeks.
The X-34 was expected in early 2000 to undergo testing in New Mexico, California, and Florida. The first of three X-34 vehicles, a structural test vehicle designated A-1, began captive-carry flights at Edwards Air Force Base, California, in June 1999. Technicians from Dryden Flight Research Center, Edwards, California, have assisted in upgrading the A-1 vehicle with structural modifications and integrating avionics, hydraulics, landing gear, and other hardware needed to turn it into a flight vehicle--now known as A-1A--for unpowered glide tests in New Mexico. Following a series of tow tests on the ground at Dryden, the X-34 A-1A will be used to conduct unpowered test flights at the U.S. Army�s White Sands Missile Range, New Mexico, according to plans current in early 2000. This test series was expected to use Orbital�s L-1011 carrier aircraft to air-launch the X-34. Powered flights, using the second and third vehicle (designated A-2 and A-3 respectively), are scheduled to be conducted at the Dryden Flight Research Center, California, and the Kennedy Space Center, Florida. The X-34 vehicle A-3 was expected in early 2000 to be brought to Dryden for envelope expansion to the maximum capability of an approximate speed of Mach 8 and altitude of 250,000 feet. Plans called for A-3 to explore additional reusable launch vehicle technologies as carry-on experiments. Dryden�s project manger was Seunghee Lee as of early 2000.
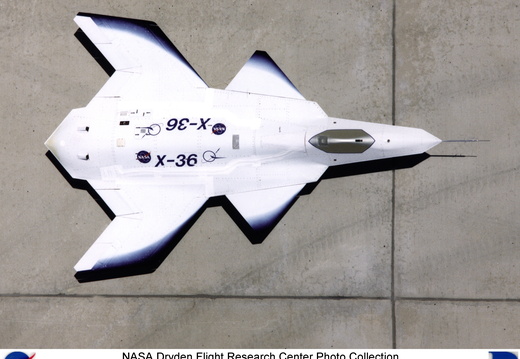
X-36
For 31 flights during 1997 at the Dryden Flight Research Center, Edwards, California, the project team examined the aircraft’s agility at low speed / high angles of attack and at high speed / low angles of attack. The aircraft’s speed envelope reached up to 206 knots (234 mph). This aircraft was very stable and maneuverable. It handled very well.
The X-36 vehicle was designed to fly without the traditional tail surfaces common on most aircraft. Instead, a canard forward of the wing was used as well as split ailerons and an advanced thrust-vectoring nozzle for directional control. The X-36 was unstable in both pitch and yaw axes, so an advanced, single-channel digital fly-by-wire control system (developed with some commercially available components) was put in place to stabilize the aircraft.
Using a video camera mounted in the nose of the aircraft and an onboard microphone, the X-36 was remotely controlled by a pilot in a ground station virtual cockpit. A standard fighter-type head-up display (HUD) and a moving-map representation of the vehicle’s position within the range in which it flew provided excellent situational awareness for the pilot. This pilot-in-the-loop approach eliminated the need for expensive and complex autonomous flight control systems and the risks associated with their inability to deal with unknown or unforeseen phenomena in flight.
Fully fueled the X-36 prototype weighed approximately 1,250 pounds. It was 19 feet long and three feet high with a wingspan of just over 10 feet. A Williams International F112 turbofan engine provided close to 700 pounds of thrust. A typical research flight lasted 35 to 45 minutes from takeoff to touchdown. A total of 31 successful research flights were flown from May 17, 1997, to November 12, 1997, amassing 15 hours and 38 minutes of flight time. The aircraft reached an altitude of 20,200 feet and a maximum angle of attack of 40 degrees.
In a follow-on effort, the Air Force Research Laboratory (AFRL), Wright-Patterson Air Force Base, Ohio, contracted with Boeing to fly AFRL's Reconfigurable Control for Tailless Fighter Aircraft (RESTORE) software as a demonstration of the adaptability of the neural-net algorithm to compensate for in-flight damage or malfunction of effectors, such as flaps, ailerons and rudders. Two RESTORE research flights were flown in December 1998, proving the viability of the software approach.
The X-36 aircraft flown at the Dryden Flight Research Center in 1997 was a 28-percent scale representation of a theoretical advanced fighter aircraft. The Boeing Phantom Works (formerly McDonnell Douglas) in St. Louis, Missouri, built two of the vehicles in a cooperative agreement with the Ames Research Center, Moffett Field, California.
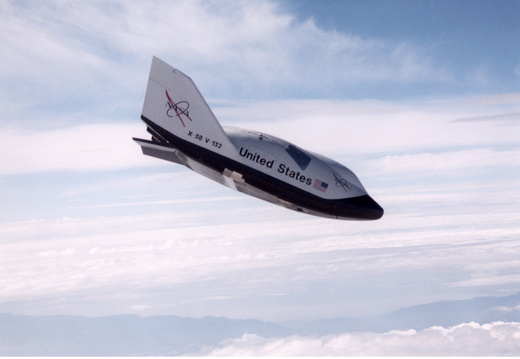
X-38
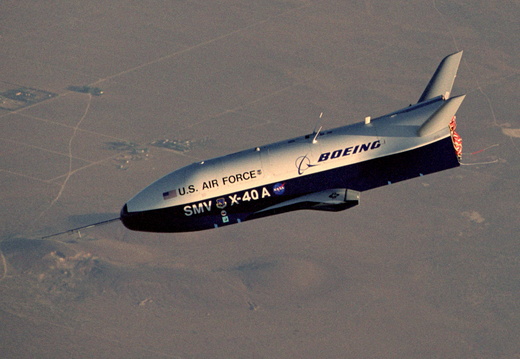
X-40
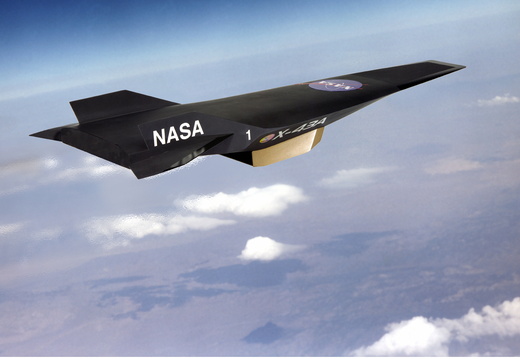
X-43
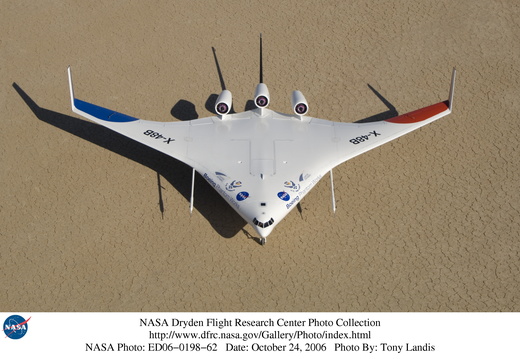
X-48B
In addition to hosting the X-48B flight test and research activities, NASA provided engineering and technical support -- expertise garnered from years of operating cutting-edge air vehicles. NASA assisted with the hardware and software validation and verification process, the integration and testing of the aircraft's systems and the pilot's ground control station. NASA's range group provided critical telemetry and command and control communications during the flight, while flight operations provided a T-34 chase aircraft and essential flight scheduling. Photo and video support completed the effort.
Boeing's Phantom Works designed the X-48B flight test vehicles in cooperation with NASA and the U.S. Air Force Research Laboratory at Wright Patterson Air Force Base, Ohio, to gather detailed information about the stability and flight-control characteristics of the blended wing body design, especially during takeoffs and landings.
The Boeing blended wing body design resembles a flying wing, but differs in that the wing blends smoothly into a wide, flat, tailless fuselage. This fuselage blending provides additional lift with less drag compared to a circular fuselage, translating to reduced fuel use at cruise conditions. Since the engines mount high on the back of the aircraft, there is less noise inside and on the ground when it is in flight.
Three turbojet engines enable the composite-skinned, 8.5 percent scale vehicle to fly up to 10,000 feet and 120 knots in its low-speed configuration. The aircraft is flown remotely from a ground control station in which the pilot uses conventional aircraft controls and instrumentation while looking at a monitor fed by a forward-looking camera on the aircraft.
NASA long has supported the development of the blended wing body shape and concept, participating in numerous collaborations with Boeing on vehicle design and analysis, as well as several wind tunnel entries of various sizes and design models.
NASA is interested in the potential benefits of the aircraft: increased volume for carrying capacity, efficient aerodynamics for reduced fuel burn and possibly significant reductions in noise due to propulsion integration options.
Two X-48B research vehicles were built by Cranfield Aerospace Ltd., in Bedford, England, in accordance with Boeing requirements. The vehicle that flew on July 20 is Ship 2, which also was used for ground and taxi testing. Ship 1, a duplicate, completed extensive wind tunnel testing in 2006 at the Full-Scale Tunnel at NASA's Langley Research Center in Hampton, Va.

XF-92A
Convair and the U.S. Air Force flew the XF-92A from 1948 to 1953. After the Air Force's plans for an interceptor failed to materialize, the NACA High-Speed Flight Research Station, which had supplied engineering, instrumentation, and operational assistance to the Air Force during its flights, took over the flight test program in 1953. A. Scott Crossfield flew all 25 NACA flights of the NACA’s XF-92A program over a six-month test period.
The original XF-92A ship had a severe pitch-up problem but was tested with different wing-fence combinations to gather data on their contribution to solving that problem. The pilot also reported that the aircraft was sluggish and underpowered. Besides validating the thin delta wing principle, the XF-92A played a major role in supporting the development of the Convair F-102A interceptor, the Air Force’s first attempt at an all-weather, supersonic interceptor. In 1953, the XF-92A experienced a landing gear failure on rollout after landing at the NACA High-Speed Research Station and the aircraft was retired.
The single-place XF-92A airplane had a delta wing swept at 60 degrees. It was 48.2 feet long, had a 31.3-foot wingspan, and was 17.5 feet high at the tip of the vertical stabilizer. It was controlled by a conventional rudder and full-span elevons that functioned as elevators and ailerons.
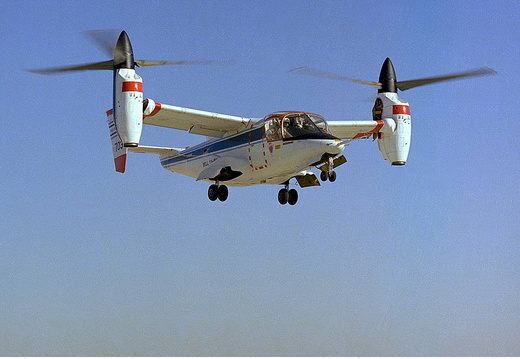
XV-15
The development of the XV-15 Tiltrotor research aircraft was initiated in 1973 with joint Army/NASA funding as a "proof of concept", or "technology demonstrator" program, with two aircraft being built by Bell Helicopter Textron (BHT) in 1977.
The aircraft are powered by twin Lycoming T-53 turboshaft engines that are connected by a cross-shaft and drive three-bladed, 25 ft diameter metal rotors (the size extensively tested in a wind tunnel). The engines and main transmissions are located in wingtip nacelles to minimize the operational loads on the cross-shaft system and, with the rotors, tilt as a single unit.
For takeoff, the proprotors and their engines are used in the straight-up position where the thrust is directed downward. The XV-15 then climbs vertically into the air like a helicopter. In this VTOL mode, the vehicle can lift off and hover for approximately one hour.
Once off the ground, the XV-15 has the ability to fly in one of two different modes. It can fly as a helicopter, in the partially converted airplane mode. The XV-15 can also then convert from the helicopter mode to the airplane mode. This is accomplished by continuous rotation of the proprotors from the helicopter rotor position to the conventional airplane propeller position. During the ten to fifteen second conversion period, the aircraft speed increases and lift is transferred from the rotors to the wing. To land, the proprotors are rotated up to the helicopter rotor position and flown as a helicopter to a vertical landing.
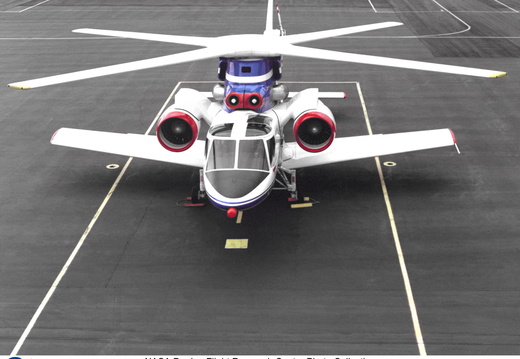
X-Wing
The unusual aircraft that resulted from the Ames Research Center/Army X-Wing Project was flown at the Ames-Dryden Flight Research Facility (now Dryden Flight Research Center), Edwards, California, beginning in the spring of 1984, with a follow-on program beginning in 1986. The program, was conceived to provide an efficient combination of the vertical lift characteristic of conventional helicopters and the high cruise speed of fixed-wing aircraft. It consisted of a hybrid vehicle called the NASA/Army Rotor Systems Research Aircraft (RSRA), which was equipped with advanced X-wing rotor systems.
The program began in the early 1970s to investigate ways to increase the speed of rotor aircraft, as well as their performance, reliability, and safety. It also sought to reduce the noise, vibration, and maintenance costs of helicopters. Sikorsky Aircraft Division of United Technologies Laboratories built two RSRA aircraft. NASA’s Langley Research Center, Hampton, Virginia, did some initial testing and transferred the program to Ames Research Center, Mountain View, California, for an extensive flight research program conducted by Ames and the Army.
The purpose of the 1984 tests was to demonstrate the fixed-wing capability of the helicopter/airplane hybrid research vehicle and explore its flight envelope and flying qualities. These tests, flown by Ames pilot G. Warren Hall and Army Maj (soon promoted to Lt. Col.) Patrick Morris, began in May and continued until October 1984, when the RSRA vehicle returned to Ames. The project manager at Dryden for the flights was Wen Painter. These early tests were preparatory for a future X-Wing rotor flight test project to be sponsored by NASA, the Defense Advanced Research Projects Agency (DARPA), and Sikorsky Aircraft.
A later derivative X-Wing flew in 1987. The modified RSRA was developed to provide a vehicle for in-flight investigation and verification of new helicopter rotor-system concepts and supporting technology. The RSRA could be configured to fly as an airplane with fixed wings, as a helicopter, or as a compound vehicle that could transition between the two configurations. NASA and DARPA selected Sikorsky in 1984 to convert one of the original RSRAs to the new demonstrator aircraft for the X-Wing concept.
Developers of X-Wing technology did not view the X-Wing as a replacement for either helicopters (rotor aircraft) or fixed-wing aircraft. Instead, they envisioned it as an aircraft with special enhanced capabilities to perform missions that call for the low-speed efficiency and maneuverability of helicopters combined with the high cruise speed of fixed-wing aircraft. Some such missions include air-to-air and air-to-ground tactical operations, airborne early warning, electronic intelligence, antisubmarine warfare, and search and rescue.
The follow-on X-Wing project was managed by James W. Lane, chief of the RSRA/X-Wing Project Office, Ames Research Center. Coordinating the Ames-Dryden flight effort in 1987 was Jack Kolf. The X-Wing project was a joint effort of NASA-Ames, DARPA, the U.S. Army, and Sikorsky Aircraft, Stratford, Connecticut. The modified X-Wing aircraft was delivered to Ames-Dryden by Sikorsky Aircraft on September 25, 1986. Following taxi tests, initial flights in the aircraft mode without main rotors attached took place at Dryden in December 1997. Ames research pilot G. Warren Hall and Sikorsky’s W. Richard Faull were the pilots. The contract with Sikorsky ended that month, and the program ended in January 1988.
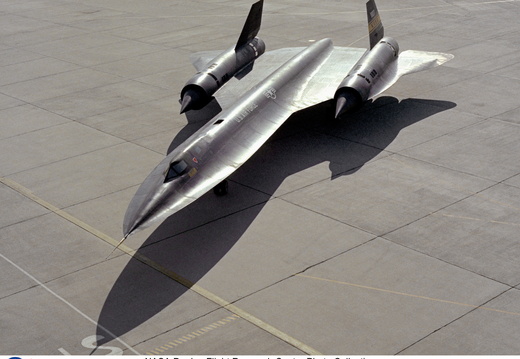
YF-12
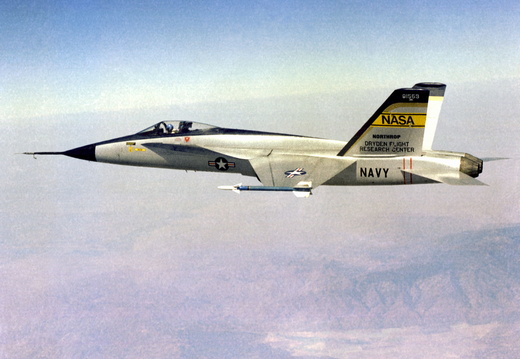
YF-17
Also studied were stability and control and buffeting at high angles of attack as well as handling qualities at high load factors. Another objective of this program was to familiarize center pilots with the operation of advanced high-performance fighter aircraft. During the seven-week program, all seven of the center’s test pilots were able to fly the aircraft with Gary Krier serving as project pilot.
In general the pilots reported no trouble adapting to the aircraft and reported that it was easy to fly. There were no familiarization flights. All 25 research flights were full-data flights. They obtained data on afterbody pressures, vertical-fin dynamic loads, agility, pilot physiology, and infrared signatures. Average flight time was 45 minutes, although two flights involving in-flight refueling lasted approximately one hour longer than usual. Dryden Project Manager Roy Bryant considered the program a success. Center pilots felt that the aircraft was generations ahead of then current active military aircraft. Originally built for the Air Force’s lightweight fighter program, the YF-17 Cobra left Dryden to support the Northrop/Navy F-18 Program. The F-18 Hornet evolved from the YF-17.
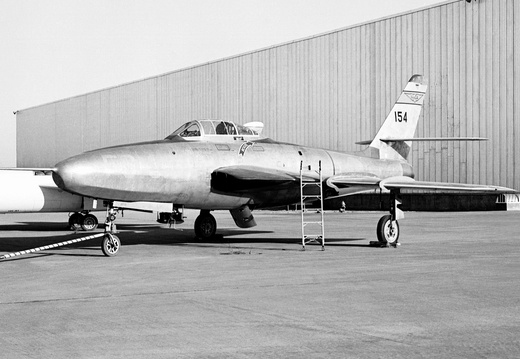
YF-84A
Republic Aviation Corporation built P-84 Thunderjets in the 1940s. The Thunderjets were the last of the subsonic straight-wing fighter-bombers to see operational service. It was the aircraft with which flight-refueling techniques for fighters was developed. The first fifteen P-84 production aircraft were fitted with Allison J35A-15 engines and designated YF-84As. (Note: In 1948
aircraft belonging to the newly independent United States Air Force went through a change in designation for the new production aircraft. The P [pursuit] became F [fighter] with the Y, indicating service test of a prototype aircraft).
Flight tests using the YF-84F Thunderstreak (49-2430) on loan from the Air Force studied the aileron effectiveness of the aircraft before spoilers were incorporated. There were two designations of this aircraft, both swept wings; the YF-84F having the inlet in the nose and the YRF-84F having the nose area elongated for cameras then faired, moving the inlets into the sides of fuselage just ahead of the wings with two fences installed on each wing for improved airflow. The "R" stood for reconnaissance. The YRF-84F was flown on research missions, chase for other research flights and for pilot proficiency.
The YF-84A (NACA #134) was used for research studies, pilot proficiency flights, and chase for other research flights while the YF-84A (45-59488) supplied the spare parts for for #134 to remain flying.
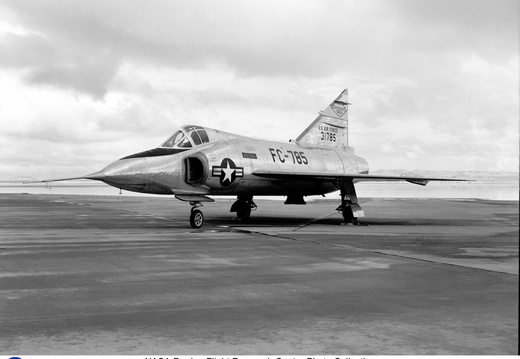
YF-102
The Convair YF-102 Delta Dagger interceptor was a scaled-up version of the delta-wing XF-92A. The NACA High-Speed Flight Station received the YF-102 in 1954 and flew it 104 times over four years. The YF-102, with a delta wing similar to the XF-92A, faced major redesign work due to pitch-up problems. Research data from wing fences used on the XF-92A was applied to the design of the YF-102. The nose inlet was changed to two side mounted inlets and the canopy was redesigned. This aircraft with
a Serial # 53-1785 and a NACA designation of #785 was retired to Edwards Air Force Base Salvage in 1958.
A modified YF-102 aircraft designated JF-102A (J stands for special test status 1956 to 1966) arrived at the NACA High-Speed Flight Station, while testing continued on the first YF-102, in 1956. The most prominent new feature of the modified vehicle was
a longer fuselage with a pinched or "coke-bottle" waist, the first application of "Area rule" developed at NACA by Richard Whitcomb (Langley Research Center). The wing had been changed to take on a conical wing camber (curvature) from research performed at the NACA Ames Aeronautical Laboratory. Before NASA ended the JF-102A program in 1959, tests pilots Jack
McKay and Neil Armstrong flew a series of landing approaches under various lift-to-drag and power conditions in preparation for the ill-fated Dyna-Soar (X-20) program. The JP-102A made 48 flights for testing performance on a delta-wing starting in 1956 and retiring in 1959 to Davis-Monthan Air Force Base, in Arizona.
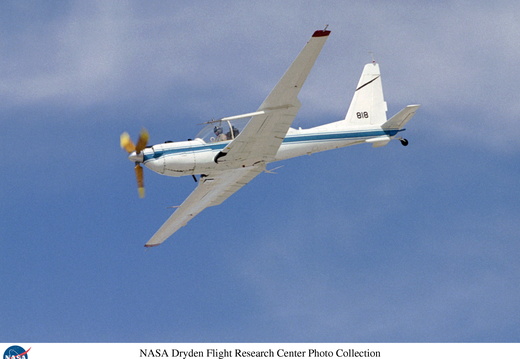
YO-3A
The YO-3A aircraft was originally a Schweizer SGS-2-32 sailplane. During the late 1960s Lockheed modified over a dozen of these sailplanes to create ultra-quiet observation aircraft for use over South Vietnam. This particular YO-3A flew combat missions and was later sold to an airframe and powerplant mechanics school.
NASA's Ames Research Center at Mountain View, California, acquired the aircraft from the school in 1978. It restored the YO-3A to flight status and fitted it with wing- and tail-mounted microphones as an acoustic research aircraft. Ames operated it at Edwards Air Force Base for noise measurements of helicopters and tilt rotor aircraft. One set of tests in December 1995 obtained free-flight noise data on the XV-15 tilt rotor.
NASA also used the YO-3A for sonic boom measurements of a NASA SR-71 assigned to the Dryden Flight Research Center. NASA transferred the YO-3A to Dryden in December 1997 and the aircraft was placed in flyable storage for nearly seven years. It was then restored to flight status in mid-2004. This involved replacing the old hoses, belts, and tires on the aircraft. The YO-3A was then returned to Ames in October 2004, where it will be used for acoustic measurements of helicopters and rotorcraft.
The designation YO-3A indicates that this aircraft was a pre-production (Y) observation (O) aircraft. Even though the YO-3A saw operational use, the Y designation was never removed. Its 210-horsepower Continental V-6 was modified to reduce noise. The engine was connected to a propeller through a belt-driven reduction system. This reduced the propeller's rotation speed. The propeller blades themselves were made of birch plywood and were wider than standard propellers. The result of these modifications was an aircraft so quiet that its noise was drowned out by the background sounds.